With a heavily discontinuous mode flyback design, the transformer's ac portion of current can be larger than the dc portion. When a high perm material is used for the transformer core, the required gap can be quite large in order to reach the low composite permeability required while the core size will likely be driven by winding and core loss considerations rather than just simply avoiding saturation.
For flyback & boost applications, powder cores such as Kool-mu, Xmu, etc... are usually best performing and lowest cost. Even these may need to be gapped and if CCM operation is required, a "stepped-gap" is preferred to allow a large load compliance. Center stepped gaps reduce the fringe flux greatly as there is never a complete gap, only localized saturation.
Determination of required grounding impedance is based on determination of coefficient of grounding which represents ratio of maximum phase voltage at phases which aren't exposed by fault and line voltage of power network:
A graphical impedance analyzer with good phase resolution is a must. Some brands have all the bells and whistles, but not the phase resolution necessary to accurately measure high Q (100+) components over the instrument's full frequency range (which should extend at least into the low megahertz).
Paralleling IGBT modules where the IGBT but not the diode has a PTC is commonly done at higher powers. I personally have never done more than 3 x 600A modules in parallel but if you look at things like high power wind then things get very "interesting". It is all a matter of analysis, good thermal coupling, symmetrical layout and current de-rating.
We get at the poles of the system by looking at the characteristic equation, 1+T(s). Unfortunately, we don't have the math available (except in classroom exercises) we have an empirical system that may or may not be reduced to a mathematical model. For power supplies, even if they can be reduced to a model, it is approximate and just about always has significant deviations from the hardware. That is why measurements persist in this industry.
As a mathematical tool eventually, simulation can help to quickly approach the results that we need. If everything is done in right way, simulation can give us reliable conductive EMI results at the low frequency range.
EMI/EMC is rather a subjective topic than theoretic, but we shall look at it with start from noise prevention then noise suppression.
Prevention or design in the solution is needed to concentrate on noise making part/component or its mechanism play in the circuit. These are referring to those part and circuit that directly involve in switching, like PFC mosfet and its driver, PFC diode, DC/DC switching mosfet and its driver, and its output diode, do not left out the magnetic part and layout design, bad design will cause ugly switching then give you headache in EMC problem.
There are several issues at work here. For high AC current inductors, you want to have low core losses, low proximity loss in the windings, and low fringing effects.
At normal frequencies, ferrites are by far the lowest core loss, much better than MPP and other so called "low-loss" materials. So you would like to use them from this aspect.
The term creepage distance is specifically associated with porcelain insulators used in the Air Insulated substations. Insulator surface attracts dust, pollution (in industrial areas) and salt (along the sea coast) and these form a conducting layer on the surface of the insulator body when the surface is wet.
1. To reduce the manpower & the CTC due to them.
2. Few skilled technicians can run the automated machines smoothly, with much lesser number of errors & faults (as human is not directly controlling every thing & is not burdened with multitasking challenge for extended duration which causes fatigue and hence errors/faults)
2. Few skilled technicians can run the automated machines smoothly, with much lesser number of errors & faults (as human is not directly controlling every thing & is not burdened with multitasking challenge for extended duration which causes fatigue and hence errors/faults)
Cross regulation is a very important component of multiple outputs. This can be done in several ways: transformer coupling, mutually coupled output filter chokes (forward-mode) and/or shared output sensing voltages/currents. All, of which, are impossible to model.
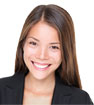
Featured
Like pumps, fans consume significant electrical energy while serving several applications. In many plants, the VFDs (variable ...
A frequency inverter controls AC motor speed. The frequency inverter converts the fixed supply frequency (60 Hz) to a ...
Motor starter (also known as soft starter, motor soft starter) is a electronic device integrates soft start, soft stop, ...
Soft starter allows the output voltage decreases gradually to achieve soft stop, in order to protect the equipment. Such as the ...
Soft Starter reduces electric motor starting current to 2-4 times during motor start up, reduces the impact to power grid during ...

In Discussion