Advantages: Clearly, this Special Protection System saved the day, and
bought time until an additional line was added 4 years later.
Disadvantages: The downside was the challenge of installing and testing such a complicated scheme with the potential for mis-operation. I don't recall any mis-operations occurring, but it was still a bit "dicey". I have been at that same plant during a full load unit trip (Generator differential) and it was an "exciting" experience to say the least! While I did recommend that we conduct a "live test" to see what would really happen and perhaps test our system BLACK START procedures, this suggestion was not well received by management (LOL).
Disadvantages: The downside was the challenge of installing and testing such a complicated scheme with the potential for mis-operation. I don't recall any mis-operations occurring, but it was still a bit "dicey". I have been at that same plant during a full load unit trip (Generator differential) and it was an "exciting" experience to say the least! While I did recommend that we conduct a "live test" to see what would really happen and perhaps test our system BLACK START procedures, this suggestion was not well received by management (LOL).
When synchronous generators (alternators) are connected in parallel with
each other on an AC grid, they are all operating at a speed that is
directly proportional to the frequency of the AC grid. No generator can
go faster or slower than the speed which is proportional to the
frequency.
That is, when a synchronous generator and its prime mover is operated in parallel with other synchronous generators and their prime movers, the speed of all of the generator rotors (and hence their prime movers if directly coupled to the generator rotors) is fixed by the frequency of the grid. If the grid frequency goes up, the speed of all the generator rotors goes up at the same time. Conversely, if the grid frequency goes down, the speed of all the generator rotors goes down at the same time. It is the job of the grid/system operators to control the amount of generation so that it exactly matches the load on the system so that the frequency remains relatively constant.
That is, when a synchronous generator and its prime mover is operated in parallel with other synchronous generators and their prime movers, the speed of all of the generator rotors (and hence their prime movers if directly coupled to the generator rotors) is fixed by the frequency of the grid. If the grid frequency goes up, the speed of all the generator rotors goes up at the same time. Conversely, if the grid frequency goes down, the speed of all the generator rotors goes down at the same time. It is the job of the grid/system operators to control the amount of generation so that it exactly matches the load on the system so that the frequency remains relatively constant.
The basic configuration of a variable frequency drive is as follows.
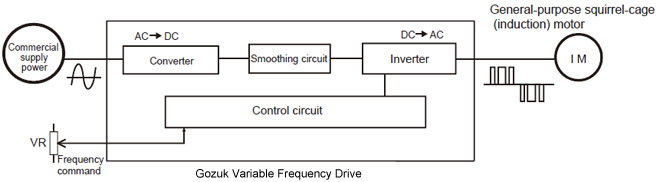
Fig. 1 Basic configuration of variable frequency drive
Each part of a variable frequency drive has the following function.
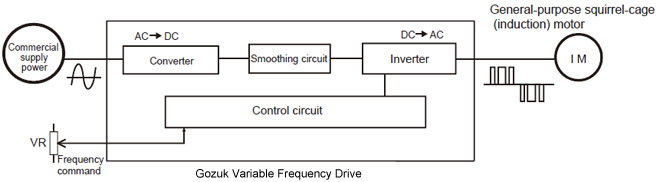
Fig. 1 Basic configuration of variable frequency drive
Each part of a variable frequency drive has the following function.
Converter: Circuit to change the commercial AC power supply to the DC
Smoothing circuit: Circuit to smooth the pulsation included in the DC
Inverter: Circuit to change the DC to the AC with variable frequency
Control circuit: Circuit to mainly control the inverter part
For the AC power line, the system (VFD + motor) is a non-linear load whose current include harmonics (frequency components multiples of the power line frequency). The characteristic harmonics generally produced by the rectifier are considered to be of order h = np±1 on the AC side, that is, on the power line (p is the number of pulses of the variable frequency drive and n =1,2,3).
Thus, in the case of a 6 diode (6 pulses) bridge, the most pronounced generated harmonics are the 5th and the 7th ones, whose magnitudes may vary from 10% to 40% of the fundamental component, depending on the power line impedance. In the case of rectifying bridges of 12 pulses (12 diodes), the most harmful harmonics generated are the 11th and the 13th ones. The higher the order of the harmonic, the lower can be considered its magnitude, so higher order harmonics can be filtered more easily. As the majority of VFD manufacturers, Gozuk produces its low voltage standard variable frequency drives with 6-pulse rectifiers.
Harmonic currents, which circulate through the power line impedances and depend on the rectifier input/output impedance values, cause harmonic voltage drops that distort the power supply voltage of the variable frequency drive and other loads connected to this line. These harmonic current and voltage distortions may increase the electrical losses in the installation, lowering the power factor and overheating components such as cables, transformers, capacitor banks, motors, etc.
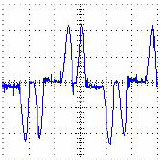
Harmonic currents, which circulate through the power line impedances and depend on the rectifier input/output impedance values, cause harmonic voltage drops that distort the power supply voltage of the variable frequency drive and other loads connected to this line. These harmonic current and voltage distortions may increase the electrical losses in the installation, lowering the power factor and overheating components such as cables, transformers, capacitor banks, motors, etc.
There are many factors that govern the performance of rotary tube furnaces. A direct fired rotary unit has a potential for much higher thermal efficiency due to the direct contact of the hot gases with the material in process. Cement kilns are the most common large scale unit operation with direct fired units. Any articles you find on this will be helpful. Thermal efficiency can be estimated by dividing the inlet temperature minus the outlet temperature by the inlet temperature minus the ambient temperature in absolute scales either Rankine or Kelvin.
A SynRM is a true AC machine with or without permanent magnets on the rotor. It is totally different from the closed-loop controlled, permanent magnet brushless DC machines (BLDC) in that one would never be able to get rid of torque ripples as that have been achieved in commonly used BLDC machines.
Stiff voltage sources are not problematic as long as they don't get in the way of the solver's attempts to linearize the behavior of the circuit matrix via step size reduction. It is the highly nonlinear stiff sources that are heavily fed back into the rest of the circuitry that can cause the solver to hang. Linear sources that are ground referenced or nonlinear ones that don't feed back anywhere are not likely to cause problems.
A low impedance fault is usually a bolted fault, which is a short circuit. It allows a high amount of fault current to flow, and an upstream breaker or fuse usually senses the high current and operates, ending the event. A high impedance fault, usually an arc fault, is a fault of too high of an impedance for overcurrent protection to detect and operate, so the fault exists for long period of time without tripping upstream protection.
Negative sequence will not cause a physical rotation. This component creates a field which, though not strong enough, tries to counter the primary field, An increase in this component will cause the motor to overheat due to the opposition. a physical rotation is not likely to occur.
After calculation of Qc, the choosing of Capacitors type will be done according to the Harmonic Distortion percentage. Noting that in some case where the Harmonic Distortion percentage is high, we should use " Detuned Reactors " with Capacitors, and when this percentage is too high, we can't install the Capacitors before minimizing or eliminating the harmonics that their percentages are too high.
The UPS systems commissioning test and inspection procedures are to conform to;
• BS EN 50091-1:1993 - Specification for Uninterruptible Power Supplies (UPS). General and Safety Requirements, AND
• IEC 62040-3 (Draft Edition – 2) in particular the Efficiency test procedures outlined in its "Annexure-J".
The biggest differences between the floor programmer and the office programmer is often a piece of paper (knowledge and experience do not replace a piece of paper in the mind of HR person that has no understanding of the position they are seeking to fill) and that the floor programmer must produce a working machine.
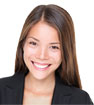
Featured
Like pumps, fans consume significant electrical energy while serving several applications. In many plants, the VFDs (variable ...
A frequency inverter controls AC motor speed. The frequency inverter converts the fixed supply frequency (60 Hz) to a ...
Motor starter (also known as soft starter, motor soft starter) is a electronic device integrates soft start, soft stop, ...
Soft starter allows the output voltage decreases gradually to achieve soft stop, in order to protect the equipment. Such as the ...
Soft Starter reduces electric motor starting current to 2-4 times during motor start up, reduces the impact to power grid during ...

In Discussion
VFD used as main power supply question
How to select a breaker??
Vibration in Vertical Pumps
Determine the effect of reduced power factor on the real power consumption
Convert 3 phase motor into 1 phase motor?
Advantages/Disadvantages of String inverters vs. Central inverters?
Hipot testing of Electric Machines
Insulation Resistance of generator stator drops
How to select a breaker??
Vibration in Vertical Pumps
Determine the effect of reduced power factor on the real power consumption
Convert 3 phase motor into 1 phase motor?
Advantages/Disadvantages of String inverters vs. Central inverters?
Hipot testing of Electric Machines
Insulation Resistance of generator stator drops