A completely sensor-less control would be completely open-loop, which isn't reliable with some motors like PMSMs. Even if you knew the switching instants for one ideal case, too many "random" variables could influence the system (just think of the initial position), so that those firing instants could be inappropriate for other situations.
Having lead design efforts for very sensitive instrumentation with high frequency A/D converters with greater than 20-bits of resolution my viewpoint is mainly concerned about the noise in the regulated supply output. In these designs fairly typical 50-mV peak-to-peak noise is totally unacceptable and some customers cannot stand 1-uVrms noise at certain frequencies.
The way around all the disadvantages is to use a doubly fed induction generator (DFIG). In addition to the stator connection to the load, the wound rotor is provided with a varying AC field whose frequency is tightly controlled through smart electronics so that a relatively fixed controllable output voltage and frequency can be achieved despite the varying speed of the prime mover and the load.
Hazardous area classification has three basic components:
Class (1,2) : Type of combustible material (Gas or Dust)
Div (I, II) : Probability of combustible material being present
Gas Group (A,B,C,D): most combustible to least combustible (amount of energy required to ignite the gas)
Class (1,2) : Type of combustible material (Gas or Dust)
Div (I, II) : Probability of combustible material being present
Gas Group (A,B,C,D): most combustible to least combustible (amount of energy required to ignite the gas)
Often, in automation, engineers will use a PLC or DCS with standard I/O, valves, servos, photo-eyes, VFDs, RTDs, etc to accomplish this task. Control engineering falls under the same umbrella in that you are automating a process such as controlling the focus on a camera or maintaining the speed of a car with a gas pedal.
We used four huge 5KV motors and VFDs at the coal mine compared to a single 0.75 HP 480 VAC VFD at the bakery, and startups/shutdowns were order of magnitudes different, but the time frame was immaterial to what the controls had to do and the techniques I applied to do the job.
The PPE (Personal Protective Equipment) requirements to work on live electrical equipment is making doing commissioning, startup, and tuning of electrical control systems awkward and cumbersome. We are at a stage where the use of PPE is now required but practice has not caught up with the requirements. While many are resisting this change, it seems inevitable that we will need to wear proper PPE equipment when working on any control panel with exposed voltages of 50 volts or more.
Grounding impedance of the transformer and building ground rods is mainly for voltage stabilization and under normal conditions should have nothing to do with our return ground fault current. See NEC 250.1 (5) "The earth shall not be considered as an effective ground-fault current path."
Manufacturers are able to achieve exceptional density by virtue of High frequency resonant topologies, but they have to achieve high efficiencies too; Else, they will generate so much heat that they cannot meet UL/IEC safety requirements.
In some cases, they will leave the thermal problem to the user. Usually, the first few paragraphs of any reference design discusses the tradeoffs.
We can see that the hysteretic controller is a special case of other control techniques. For example, "sliding mode control" usually uses two state variables to determine one switching variable (switch ON or OFF). So the hysteretic controller is a special case of "1-dimensional" sliding mode.
There are three different more or less widely used types of constant on-time control. The first one is where the off-time is varied with an error signal. A loop with this type of control has a control-to-output voltage frequency response (or Bode plot if you prefer) similar to that of the constant-frequency voltage-mode control.
Very few know about the Right Half Plane Pole (not a RHP-Zero) at high duty cycle in a DCM buck with current mode control. Maybe because it is not really a problem.
It is said that this instability starts above 2/3 duty cycle – I think that must be with a resistive load. If loaded with a pure current source, it starts above 50% duty cycle.
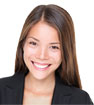
Featured
Like pumps, fans consume significant electrical energy while serving several applications. In many plants, the VFDs (variable ...
A frequency inverter controls AC motor speed. The frequency inverter converts the fixed supply frequency (60 Hz) to a ...
Motor starter (also known as soft starter, motor soft starter) is a electronic device integrates soft start, soft stop, ...
Soft starter allows the output voltage decreases gradually to achieve soft stop, in order to protect the equipment. Such as the ...
Soft Starter reduces electric motor starting current to 2-4 times during motor start up, reduces the impact to power grid during ...

In Discussion
Electrical shock prevent system in case of firefight operation for roof projects
Outdoor application
Flyback design
how can we reduce the flash steam in condensate tank?
Is Software Defined Networking the Future of Cloud & Network Infrastructure?
Classification of Hazardous Areas - Biodiesel Vacuum Distillation
How does unbalanced loading systems affect prepaid metering?
Transformer tripping
Outdoor application
Flyback design
how can we reduce the flash steam in condensate tank?
Is Software Defined Networking the Future of Cloud & Network Infrastructure?
Classification of Hazardous Areas - Biodiesel Vacuum Distillation
How does unbalanced loading systems affect prepaid metering?
Transformer tripping