Synchronous generator operating frequency
When synchronous generators (alternators) are connected in parallel with each other on an AC grid, they are all operating at a speed that is directly proportional to the frequency of the AC grid. No generator can go faster or slower than the speed which is proportional to the frequency.
That is, when a synchronous generator and its prime mover is operated in parallel with other synchronous generators and their prime movers, the speed of all of the generator rotors (and hence their prime movers if directly coupled to the generator rotors) is fixed by the frequency of the grid. If the grid frequency goes up, the speed of all the generator rotors goes up at the same time. Conversely, if the grid frequency goes down, the speed of all the generator rotors goes down at the same time. It is the job of the grid/system operators to control the amount of generation so that it exactly matches the load on the system so that the frequency remains relatively constant.
Isolated or is landed generators that are not in parallel with other generators have an added limitation in that keeping exactly 50Hz is somewhat difficult, or puts too much demand on controlling/governing systems. In such environments it is normal to accept some small deviation from the nominal frequency.
The vast majority of power for industry is supplied by large rotating AC generators turning in synch with the frequency of the grid. The frequency of all these generators will be identical and is tied directly to the RPM of the generators themselves. If there is sufficient power in the generators then the frequency can be maintained at the desired rate (i.e. 50Hz or 60Hz depending on the locale).
An increase in the power load is accompanied by a concurrent increase in the power supplied to the generators, generally by the governors automatically opening a steam or gas inlet valve to supply more power to the turbine. However, if there is not sufficient power, even for a brief period of time, then generator RPM and the frequency drops.
By operating transformers at higher frequencies, they can be physically more compact because a given core is able to transfer more power without reaching saturation and fewer turns are needed to achieve the same impedance. However, properties such as core loss and conductor skin effect also increase with frequency. Aircraft and military equipment employ 400 Hz power supplies which reduce core and winding weight. Operation of a transformer at its designed voltage but at a higher frequency than intended will lead to reduced magnetizing current. At a lower frequency, the magnetizing current will increase. Operation of a transformer at other than its design frequency may require assessment of voltages, losses, and cooling to establish if safe operation is practical. For example, transformers may need to be equipped with 'volts per hertz' over-excitation relays to protect the transformer from overvoltage at higher than rated frequency.
That is, when a synchronous generator and its prime mover is operated in parallel with other synchronous generators and their prime movers, the speed of all of the generator rotors (and hence their prime movers if directly coupled to the generator rotors) is fixed by the frequency of the grid. If the grid frequency goes up, the speed of all the generator rotors goes up at the same time. Conversely, if the grid frequency goes down, the speed of all the generator rotors goes down at the same time. It is the job of the grid/system operators to control the amount of generation so that it exactly matches the load on the system so that the frequency remains relatively constant.
Isolated or is landed generators that are not in parallel with other generators have an added limitation in that keeping exactly 50Hz is somewhat difficult, or puts too much demand on controlling/governing systems. In such environments it is normal to accept some small deviation from the nominal frequency.
The vast majority of power for industry is supplied by large rotating AC generators turning in synch with the frequency of the grid. The frequency of all these generators will be identical and is tied directly to the RPM of the generators themselves. If there is sufficient power in the generators then the frequency can be maintained at the desired rate (i.e. 50Hz or 60Hz depending on the locale).
An increase in the power load is accompanied by a concurrent increase in the power supplied to the generators, generally by the governors automatically opening a steam or gas inlet valve to supply more power to the turbine. However, if there is not sufficient power, even for a brief period of time, then generator RPM and the frequency drops.
By operating transformers at higher frequencies, they can be physically more compact because a given core is able to transfer more power without reaching saturation and fewer turns are needed to achieve the same impedance. However, properties such as core loss and conductor skin effect also increase with frequency. Aircraft and military equipment employ 400 Hz power supplies which reduce core and winding weight. Operation of a transformer at its designed voltage but at a higher frequency than intended will lead to reduced magnetizing current. At a lower frequency, the magnetizing current will increase. Operation of a transformer at other than its design frequency may require assessment of voltages, losses, and cooling to establish if safe operation is practical. For example, transformers may need to be equipped with 'volts per hertz' over-excitation relays to protect the transformer from overvoltage at higher than rated frequency.
You may also like:
Soft starters and variable frequency drives are two different purpose products. VFD is for AC motor speed control, it's not only change the output voltage but also change the frequency; Soft starter is a ...
From a manufacturing economics standpoint, there is often a trade off in the decision to add a DC bus choke or not based on its ability to reduce the DC bus ripple. This is because it can reduce the DC bus ...
I had small hills of dead MOSFETs and the directly attached controllers. When the first power MOSFETs emerged in 1979, I blew-up so many that I almost wrote them off. They had some real issues with D-S voltage ...
Overcurrent protection uses as back-up protection for protection generators from faults between two windings of stator (two phases of stator). Setting of overcurrent protection depends from two settings: ...
Non-regenerative DC drives, also known as single-quadrant drives, rotate in one direction only & they have no inherent braking capabilities. Stopping the motor is done by removing voltage & allowing ...
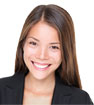
Featured
Like pumps, fans consume significant electrical energy while serving several applications. In many plants, the VFDs (variable ...
A frequency inverter controls AC motor speed. The frequency inverter converts the fixed supply frequency (60 Hz) to a ...
Motor starter (also known as soft starter, motor soft starter) is a electronic device integrates soft start, soft stop, ...
Soft starter allows the output voltage decreases gradually to achieve soft stop, in order to protect the equipment. Such as the ...
Soft Starter reduces electric motor starting current to 2-4 times during motor start up, reduces the impact to power grid during ...

In Discussion
Lighting wires(120V) and control cable(12 V)
earthing design
what is difference between grounding and earthing?
grounding
Non Contact sensor to detect direction of rotation of Fan blades
The smaller dimensions motors are in efficient
3 phase AC/DC flyback input series resistor
how the mirrors of solar panels move, to stay in the direction of the sun?
earthing design
what is difference between grounding and earthing?
grounding
Non Contact sensor to detect direction of rotation of Fan blades
The smaller dimensions motors are in efficient
3 phase AC/DC flyback input series resistor
how the mirrors of solar panels move, to stay in the direction of the sun?