Simulator history
Power electronics has always provided a special challenge for simulation. As Hamish mentioned above, one of the problems encountered is inductor cutsets, and capacitor loops that lead to numerical instability in the simulation matrices.
In the 80s, Spice ran so slowly that is was not an option unless you wanted to wait hours or days for results, and frequently it failed to converge anyway. It was never intended to handle the large swings of power circuits, and coupled with the numerical problems above, was just not a feasible approach.
Ideal-switch simulations were used with other software to get rid of many of the nonlinearities of devices that slowed simulation down, but Spice really hated ideal switches as it would try to converge on the infinite slope edges.
Three universities started writing specialized software for converter simulation to address this shortcomings of Spice. Virginia Tech had COSMIR, which I helped write with a grad student, Duke University had the program which later became Simplis, and the University of Lowell had their program, the name of which I don't recall (anyone remember?).
All of these programs started before Windows came along, and they were fast and efficient. With windows, the programming overhead to maintain programs like these moved beyond the scope of what university research groups in power electronics could handle. Only the Duke program survived, with Ron Wong leading the effort at a private company. The achievements of Simplis are remarkable, but it is a massive effort to keep this program going for a relatively small marketplace (power supply companies are notoriously cheap, so the potential market does not get realized), and that keeps the price quite high. If you can afford it, you should have this program.
Spice now runs at a reasonable pace on the latest PCs, so it is back in the game. LT Spice is leading the charge because it is free, and the models are relatively rugged. Now that speed is less of a factor, you can put real switches in, and Spice can handle them in a reasonable amount of time. (Depending on your definition of "reasonable".)
PSIM was another ideal switch model, and they eliminated the convergence headaches that plagued all the other programs by not having convergence at all. You just cut the step size down to get the accuracy you needed, and this worked fine for exploring power stages and waveforms, but was not good for fast transient feedback loops. As the digital controller people quickly realized, the resolution on the PWM output needed to avoid numerical oscillations is very fine, and PSIM couldn't handle that without slowing down too much.
When I left Virginia Tech, I felt the bulk of the industry needed a fast simulation and design solution so engineers did not have to add to their burdens with worrying about convergence and other problems. This is a hardware-driven field, and we all have our hands full dealing with real life blowups that simulation just doesn't begin to predict.
I have observed in teaching over the years that engineers in a hurry to get to the hardware have very little tolerance for waiting for simulation. If you are building a well-known topology, about 2 seconds is as long as they will wait before they become impatient.
This is the gap that POWER 4-5-6 plugs. The simulation is practically instantaneous, and the program has no convergence issues so you design and simulate rapidly before moving to a breadboard. It is intended for the working engineer who is under severe time pressure, but would like some simulation to verify design integrity.
In the 80s, Spice ran so slowly that is was not an option unless you wanted to wait hours or days for results, and frequently it failed to converge anyway. It was never intended to handle the large swings of power circuits, and coupled with the numerical problems above, was just not a feasible approach.
Ideal-switch simulations were used with other software to get rid of many of the nonlinearities of devices that slowed simulation down, but Spice really hated ideal switches as it would try to converge on the infinite slope edges.
Three universities started writing specialized software for converter simulation to address this shortcomings of Spice. Virginia Tech had COSMIR, which I helped write with a grad student, Duke University had the program which later became Simplis, and the University of Lowell had their program, the name of which I don't recall (anyone remember?).
All of these programs started before Windows came along, and they were fast and efficient. With windows, the programming overhead to maintain programs like these moved beyond the scope of what university research groups in power electronics could handle. Only the Duke program survived, with Ron Wong leading the effort at a private company. The achievements of Simplis are remarkable, but it is a massive effort to keep this program going for a relatively small marketplace (power supply companies are notoriously cheap, so the potential market does not get realized), and that keeps the price quite high. If you can afford it, you should have this program.
Spice now runs at a reasonable pace on the latest PCs, so it is back in the game. LT Spice is leading the charge because it is free, and the models are relatively rugged. Now that speed is less of a factor, you can put real switches in, and Spice can handle them in a reasonable amount of time. (Depending on your definition of "reasonable".)
PSIM was another ideal switch model, and they eliminated the convergence headaches that plagued all the other programs by not having convergence at all. You just cut the step size down to get the accuracy you needed, and this worked fine for exploring power stages and waveforms, but was not good for fast transient feedback loops. As the digital controller people quickly realized, the resolution on the PWM output needed to avoid numerical oscillations is very fine, and PSIM couldn't handle that without slowing down too much.
When I left Virginia Tech, I felt the bulk of the industry needed a fast simulation and design solution so engineers did not have to add to their burdens with worrying about convergence and other problems. This is a hardware-driven field, and we all have our hands full dealing with real life blowups that simulation just doesn't begin to predict.
I have observed in teaching over the years that engineers in a hurry to get to the hardware have very little tolerance for waiting for simulation. If you are building a well-known topology, about 2 seconds is as long as they will wait before they become impatient.
This is the gap that POWER 4-5-6 plugs. The simulation is practically instantaneous, and the program has no convergence issues so you design and simulate rapidly before moving to a breadboard. It is intended for the working engineer who is under severe time pressure, but would like some simulation to verify design integrity.
You may also like:
Before breaker's selecting for your electrical system, you need to calculate value of expected short circuit current at the place of breaker's installation. Then you need to calculate value of heat pulse and ...
With regards to hazardous areas, Electrical equipment to be installed in those areas should comply with the zone classification. I believe the location where you are intending to install this motor would have ...
The industry as a whole needs to enforce better system design and performance. This initiative will come from the clients, and implemented by the developers. The cost/benefit trade-off will always be present. ...
PLC is defined as Programmable Logic Controller. It is a hardware, Includes processor, I/P & O/P Modules, Counters, Function Blocks, Timers,,, etc. The I/Os are either Analogue or Digitals or both. PLC can ...
We should select a drive (direct/flexible, chain, flat/vee/ribbed belt, gearbox, vfd, rope, close couples etc) depending on the characteristics of load(speed, torque, power, fluctuating, periodical, constant, ...
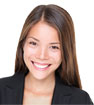
Featured
Like pumps, fans consume significant electrical energy while serving several applications. In many plants, the VFDs (variable ...
A frequency inverter controls AC motor speed. The frequency inverter converts the fixed supply frequency (60 Hz) to a ...
Motor starter (also known as soft starter, motor soft starter) is a electronic device integrates soft start, soft stop, ...
Soft starter allows the output voltage decreases gradually to achieve soft stop, in order to protect the equipment. Such as the ...
Soft Starter reduces electric motor starting current to 2-4 times during motor start up, reduces the impact to power grid during ...

In Discussion
Fundamental Power Conversion Book
Use solar power for all my electric machines in the house
Sub-panels into industrial control panels
How many square meter space do we need for 1 MWp solar Power Farm?
Mobile devices for industrial automation?
what does mean by circulating current in a transformer?
Active or Passive PFC for front end?
solar water pumping system
Use solar power for all my electric machines in the house
Sub-panels into industrial control panels
How many square meter space do we need for 1 MWp solar Power Farm?
Mobile devices for industrial automation?
what does mean by circulating current in a transformer?
Active or Passive PFC for front end?
solar water pumping system