Sensorless control
I am curious about the definition of "sensorless control". When you talk about sensorless control, are you in fact meaning a lack of physical position sensor such as e.g. a magnet plus vane plus hall effect? i.e. not having a unit whose sole objective is position detection.
Is the sensorless control based around alternative methods of measurement or detection to predict position using components that have to exist for the machine to function (such as measuring or detecting voltages or currents in the windings)?
I had long ago wondered about designing a motor, fully measuring its voltage and current profiles and phase firing timings for normal operation (from stationary to full speed full load) using a position sensor for getting the motor to work and to determine the best required phase firing sequences and associated voltage/current profiles then program a microprocessor to replicate the entire required profile such that I would attempt to eliminate the need for any sensing or measurement at all (but I concluded it would come very unstuck for any fault conditions or restarting while it was still turning). So in my mind don't all such machines require a form of measurement (i.e. some form of "sensing") to work properly so could never be truly sensorless?
A completely sensor-less control would be completely open-loop, which isn't reliable with some motors like PMSMs. Even if you knew the switching instants for one ideal case, too many "random" variables could influence the system (just think of the initial position), so that those firing instants could be inappropriate for other situations.
Actually, induction machines, thanks to their inherent stability properties, can be run really sensor-less (i.e. just connected to the grid or in V/f). To be honest, even in the simple grid-connection case there is an overcurrent detection somewhere in the grid, which requires some sensing.
But there can also be said the term sensorless relates to el. motor itself. In another words, it means there are not any sensors “attached” to the el. motor (which does not mean sensors cannot be in the inverter, in such a case). In our company we are using the second meaning, since it indicates no sensor connections are needed between the el. motor and the ECU (inverter).
Is the sensorless control based around alternative methods of measurement or detection to predict position using components that have to exist for the machine to function (such as measuring or detecting voltages or currents in the windings)?
I had long ago wondered about designing a motor, fully measuring its voltage and current profiles and phase firing timings for normal operation (from stationary to full speed full load) using a position sensor for getting the motor to work and to determine the best required phase firing sequences and associated voltage/current profiles then program a microprocessor to replicate the entire required profile such that I would attempt to eliminate the need for any sensing or measurement at all (but I concluded it would come very unstuck for any fault conditions or restarting while it was still turning). So in my mind don't all such machines require a form of measurement (i.e. some form of "sensing") to work properly so could never be truly sensorless?
A completely sensor-less control would be completely open-loop, which isn't reliable with some motors like PMSMs. Even if you knew the switching instants for one ideal case, too many "random" variables could influence the system (just think of the initial position), so that those firing instants could be inappropriate for other situations.
Actually, induction machines, thanks to their inherent stability properties, can be run really sensor-less (i.e. just connected to the grid or in V/f). To be honest, even in the simple grid-connection case there is an overcurrent detection somewhere in the grid, which requires some sensing.
But there can also be said the term sensorless relates to el. motor itself. In another words, it means there are not any sensors “attached” to the el. motor (which does not mean sensors cannot be in the inverter, in such a case). In our company we are using the second meaning, since it indicates no sensor connections are needed between the el. motor and the ECU (inverter).
You may also like:
1). Through this policy, it is a Systemic transfer of Public Property to Private Companies, despite failure of many Biomass power projects and Wind mills with a great loss of Tax collection
2). Lot of Debt ...
New improvements make a long list but one of the most recent is being able to switch a DB to and from optimised. How many times in previous versions did I forget to check the box then have to delete the DB and ...
In a balanced 3-phase system with pure sine waves, the neutral current is zero, ideally.
If there is phase imbalance, it shows up in the neutral, so check for imbalance.
The other major cause of high neutral ...
Even the humble motor car runs diagnostics that the garage read to see the problems with your car. This doesn't involve technicians looking at the code that controls the car but is 100% driven by the faults ...
We get at the poles of the system by looking at the characteristic equation, 1+T(s). Unfortunately, we don't have the math available (except in classroom exercises) we have an empirical system that may or may ...
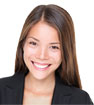
Featured
Like pumps, fans consume significant electrical energy while serving several applications. In many plants, the VFDs (variable ...
A frequency inverter controls AC motor speed. The frequency inverter converts the fixed supply frequency (60 Hz) to a ...
Motor starter (also known as soft starter, motor soft starter) is a electronic device integrates soft start, soft stop, ...
Soft starter allows the output voltage decreases gradually to achieve soft stop, in order to protect the equipment. Such as the ...
Soft Starter reduces electric motor starting current to 2-4 times during motor start up, reduces the impact to power grid during ...

In Discussion
Spur growth and demand for Electric Motors in India.
question: I am in a debate concerning motion.
Should SCADA PC, HMI, PLC, DCS be on the same existing IT NETWORK
Problems overcoming check valve on fire pump system
ONE of my diesel generator 1400kva trips down
Are there any zero installation, Windows based, stand-alone HMIs?
what is the difference of turbine impellers and propeller agitators?
Bode diagram
question: I am in a debate concerning motion.
Should SCADA PC, HMI, PLC, DCS be on the same existing IT NETWORK
Problems overcoming check valve on fire pump system
ONE of my diesel generator 1400kva trips down
Are there any zero installation, Windows based, stand-alone HMIs?
what is the difference of turbine impellers and propeller agitators?
Bode diagram