Reduce cost of single and three induction motor
First you must optimize the design for the application. This is true for the electromagnetic and mechanical design. If you are making a general purpose motor then this will be more challenging because you will have to compromise to meet a variety of requirements. But the process is the same. You can design by hand using knowledge and experience or, better you can use the numerous design tools, many of which have perimetric design, variable ranges or optimization methods.
To evaluate your designs you need a cost equation. You simply multiply the weight of material and the cost or relative cost of the materials. Can you reduce the amount of the most expensive materials by making better use of the less expensive ones. Often you can.
With a similar approach you can review the mechanical design and you must be aware the these two activities can become intertwined. It is understanding this tight interrelationship that makes a good machine designer. So you must ask are you using the materials effectively? If for example you have poor cooling, optimization of the electromagnetic design will not get you to the lowest cost machine. Don't forget about fan design, air flow, thermal transfer and similar items. Mechanical also involves the amount of material in the parts. Can the amount of material be reduced and still maintain strength? And so on...
Finally you look at presses. First are your processes themselves reducing the effectiveness of the materials. Poor processes show up in high stray losses, high iron and copper losses. Do you have a good die casting process? What is you vendor doing? Do the know and how can they help you. And sometimes you should ask them how you can help them. If you design is hard to make well, who's fault is that. Look at winding, excessive material? Insulation, to thick or thin? Do you have good contact between stator and housing?
That is no one thing that gets to a low cost design. It is like playing sports, you have to learn the fundamentals and execute them well. Once you do that, then you can look at automation, more exotic processes and materials. It is a great team project. Pull together someone with sales, electromagnetic, mechanical, and manufacturing process experience and have a go at it. It is great fun and exciting. You will be surprised at what you will find.
To evaluate your designs you need a cost equation. You simply multiply the weight of material and the cost or relative cost of the materials. Can you reduce the amount of the most expensive materials by making better use of the less expensive ones. Often you can.
With a similar approach you can review the mechanical design and you must be aware the these two activities can become intertwined. It is understanding this tight interrelationship that makes a good machine designer. So you must ask are you using the materials effectively? If for example you have poor cooling, optimization of the electromagnetic design will not get you to the lowest cost machine. Don't forget about fan design, air flow, thermal transfer and similar items. Mechanical also involves the amount of material in the parts. Can the amount of material be reduced and still maintain strength? And so on...
Finally you look at presses. First are your processes themselves reducing the effectiveness of the materials. Poor processes show up in high stray losses, high iron and copper losses. Do you have a good die casting process? What is you vendor doing? Do the know and how can they help you. And sometimes you should ask them how you can help them. If you design is hard to make well, who's fault is that. Look at winding, excessive material? Insulation, to thick or thin? Do you have good contact between stator and housing?
That is no one thing that gets to a low cost design. It is like playing sports, you have to learn the fundamentals and execute them well. Once you do that, then you can look at automation, more exotic processes and materials. It is a great team project. Pull together someone with sales, electromagnetic, mechanical, and manufacturing process experience and have a go at it. It is great fun and exciting. You will be surprised at what you will find.
You may also like:
A system I have just completed was 24 containers + 3 buildings for storage with 76 conveyors, 3 drop-off and 3 loading points. Connection to ERP system and weigh scales to weigh trucks and send them to the ...
Sometimes, lightning or lightning impulse voltage also will cause the variable frequency drive damaged. In addition, if the power supply system with a vacuum circuit breaker, short-circuit on/off will generate ...
Soft starter allows the output voltage decreases gradually to achieve soft stop, in order to protect the equipment. Such as the impact of the water pump, when the pump stops suddenly, the water flow inertia in ...
Often, in automation, engineers will use a PLC or DCS with standard I/O, valves, servos, photo-eyes, VFDs, RTDs, etc to accomplish this task. Control engineering falls under the same umbrella in that you are ...
After that he certainly never forgot this key lesson: never attempt to measure FET current by putting a current probe in its source--- put it on the drain side. It was that simple. The same unit never exploded ...
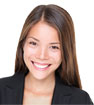
Featured
Like pumps, fans consume significant electrical energy while serving several applications. In many plants, the VFDs (variable ...
A frequency inverter controls AC motor speed. The frequency inverter converts the fixed supply frequency (60 Hz) to a ...
Motor starter (also known as soft starter, motor soft starter) is a electronic device integrates soft start, soft stop, ...
Soft starter allows the output voltage decreases gradually to achieve soft stop, in order to protect the equipment. Such as the ...
Soft Starter reduces electric motor starting current to 2-4 times during motor start up, reduces the impact to power grid during ...

In Discussion