PPE (Personal Protective Equipment)
When I think of using PPE as a controls engineer, I think
about electrical shock and arc-flash safety in working with electrical devices.
The PPE (Personal Protective Equipment) requirements to work on live electrical
equipment is making doing commissioning, startup, and tuning of electrical
control systems awkward and cumbersome. We are at a stage where the use of PPE
is now required but practice has not caught up with the requirements. While
many are resisting this change, it seems inevitable that we will need to wear
proper PPE equipment when working on any control panel with exposed voltages of
50 volts or more.
With many electrical panels not labeled for shock and arc-flash hazard levels,
the default PPE requires a full (Category 2+) suit in most cases, which is very
awkward indeed. What can we do to allow us to work on live equipment in a safe
manner that meets the now not so new requirements for shock and arc-flash
safety?
Increasingly the thinking is to design our systems for shock and arc-flash
safety. Typically low voltage (less than 50 volts), 120VAC, and 480 VAC power
were often placed in the same control enclosure. While this is cost effective,
it is now problematic when wanting to do work on even the low voltage area of
the panel. The rules do not appear to allow distinguishing areas of a panel as
safe, while another is unsafe. The entire panel is either one or the other. One
could attempt to argue this point, but wouldn't it be better to just design our
systems so that we are clearly on the side of compliance?
Here are my thoughts to improve electrical shock and arc flash safety by
designing this safety into electrical control panels.
1. Keep the power components separate from the signal level components so that
maintenance and other engineers can work on the equipment without such hazards
being present. That's the principle. What are some ideas for putting this into
practice?
2. Run as much as possible on 24VDC as possible. This would include the PLC's
and most other panel devices. A separate panel would then house only these shock
and arc-flash safe electrical components.
3. Power Supplies could be placed in a separate enclosure or included in the
main (low voltage) panel but grouped together and protected separately so that
there are no exposed conductors or terminals that can be reached with even a
tool when the control panel door is opened.
4. Motor Controls running at anything over 50 volts should be contained in a
separate enclosure. Try remoting the motor controls away from the power devices
where possible. This includes putting the HIM (keypad) modules for a VFD
(Variable Frequency Drive) for example on the outside of the control panel, so
the panel does not have to be opened. Also, using the traditional MCC (Motor
Control Centers) enclosures is looking increasing attractive to minimize the
need for PPE equipment.
For example "finger safe" design does not meet the requirements for arc-flash
safety. Also making voltage measurements to check for power is considered one
of, if not the most hazardous activity as far as arc-flash goes.
You may also like:
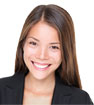
Featured

In Discussion
Communication protocol.
Why ground neutral at only one point in a voltage level?
Installation of VFD on Air Compressor
What sort of system normally used for batching purposes
Neutral line open and hazards to single phase equipments
Replacement of DC drive
Over flux Protection (V/f) for Generator Step Up Transformer.