Motor die-cast rotor non-grain-oriented VS grain-oriented
If the material is non-grain-oriented, the path of least resistance for the magnetic flux varies widely from point to point across the sheet: in one place it may go left-to-right across the sheet surface, in another top-to-bottom, and in still another through the sheet. Other points may be anywhere and everywhere in between.
If the material is grain-oriented, the material is aligned such that there is a significant reduction in the energy requirement for passing flux in one direction relative to any other.
Most machines work best with a uniform flux distribution at all points of the airgap surface: this is achieved by stacking both stator and rotor using non-grain-oriented laminations in any arrangement. However, for a grain-oriented material, each lamination has to be rotated by some angle with respect to the one above and below it in the stack (think of it like a spiral staircase).
Regardless of how the winding is made for the rotor (form wound, bar and ring, or die-cast), it is the STACKING process for the core steel that affects grain orientation.
As to skewing BOTH stator and rotor ... why? It is a more costly and complex manufacturing process to produce a skewed core vs an unskewed one, regardless whether the skew is in the rotor or stator. Once the skew is begun, there is no real cost difference between a full slot skew and a fractional slot skew.
If you really want to skew both, though - opt for a half-slot skew in one direction in the rotor, and a half-slot skew in the opposite direction for the stator. Note that this means there is only ONE way to assemble rotor and stator together - with the skews opposing. (With the full slot skew on either rotor or stator and an unskewed opposite piece, the rotor can be inserted from either end of the stator with the same effect.)
If the material is grain-oriented, the material is aligned such that there is a significant reduction in the energy requirement for passing flux in one direction relative to any other.
Most machines work best with a uniform flux distribution at all points of the airgap surface: this is achieved by stacking both stator and rotor using non-grain-oriented laminations in any arrangement. However, for a grain-oriented material, each lamination has to be rotated by some angle with respect to the one above and below it in the stack (think of it like a spiral staircase).
Regardless of how the winding is made for the rotor (form wound, bar and ring, or die-cast), it is the STACKING process for the core steel that affects grain orientation.
As to skewing BOTH stator and rotor ... why? It is a more costly and complex manufacturing process to produce a skewed core vs an unskewed one, regardless whether the skew is in the rotor or stator. Once the skew is begun, there is no real cost difference between a full slot skew and a fractional slot skew.
If you really want to skew both, though - opt for a half-slot skew in one direction in the rotor, and a half-slot skew in the opposite direction for the stator. Note that this means there is only ONE way to assemble rotor and stator together - with the skews opposing. (With the full slot skew on either rotor or stator and an unskewed opposite piece, the rotor can be inserted from either end of the stator with the same effect.)
You may also like:
Back to electronic meters, if there are transformers inside the electronic meter, placement of a magnet as close to this transformer as possible could cause over fluxing every half a cycle, this could cause a ...
There are possibilities of having inter-turn faults on the rotor winding: when the insulation positioned between adjacent conductors break (electrically) over time under certain mechanisms. These mechanisms ...
It is not easily answered since there are many variables at play which will affect the starting time. For a large medium voltage motor, it is recommended that a motor starting analysis be performed so that ...
Very few know about the Right Half Plane Pole (not a RHP-Zero) at high duty cycle in a DCM buck with current mode control. Maybe because it is not really a problem.
It is said that this instability starts ...
With a heavily discontinuous mode flyback design, the transformer's ac portion of current can be larger than the dc portion. When a high perm material is used for the transformer core, the required gap can be ...
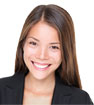
Featured
Like pumps, fans consume significant electrical energy while serving several applications. In many plants, the VFDs (variable ...
A frequency inverter controls AC motor speed. The frequency inverter converts the fixed supply frequency (60 Hz) to a ...
Motor starter (also known as soft starter, motor soft starter) is a electronic device integrates soft start, soft stop, ...
Soft starter allows the output voltage decreases gradually to achieve soft stop, in order to protect the equipment. Such as the ...
Soft Starter reduces electric motor starting current to 2-4 times during motor start up, reduces the impact to power grid during ...

In Discussion
HOW DO I BEST GO ABOUT BREAKING INTO THE SOLAR INDUSTRY
210 MW Generator Short Circuit: Cause/Reason & Analysis
Difference between industrial PLC scada & substation automation scada
Distribution system supplying electricity to residential consumers
Why would Two separate PLCs lose there programming at the same time
Synchronous Generator Insulation level
Transmission line absorb or produce reactive power
1 megawatt ground mounted solar farm from panels to the inverters?
210 MW Generator Short Circuit: Cause/Reason & Analysis
Difference between industrial PLC scada & substation automation scada
Distribution system supplying electricity to residential consumers
Why would Two separate PLCs lose there programming at the same time
Synchronous Generator Insulation level
Transmission line absorb or produce reactive power
1 megawatt ground mounted solar farm from panels to the inverters?