Load Break Switch VS Circuit Breaker
There are two important different parameters as far as the disconnection/connection of Electrical utilities is concerned.
- Breaking capacity.
- Making Capacity.
Making capacity is more higher since it is considering the initial starting current, inrush and faults that might occur at switching on moment.
Accordingly, the Circuit breakers have both while the Isolator or LBS has only breaking capacity. Isolator therefore used to isolate/disconnect/break load. To be switched on only under no load.
Basically and LBS is only designed to make and break load currents. It can be closed onto a fault (has a making rating) and cannot break a fault current. A CB is designed to make and break fault currents and off course load currents. Need to be careful with switching long cables and long lines with LBS, due to its limitation with switching cable/line charging (highly capacitive) currents. Similar precaution with needed with switching reactive loads like large transformers. Normally a CB is recommended for the 2 latter cases. Check the manufacturer test specs.
In simple way the Load Break Switch used to cut off healthy circuits or to break / disconnect the load. As a precaution, normally the LBS / Isolator are to be switched on under no load, the connected load to be utilized after switching on the Isolator. This why it has no making capacity. Circuit Breakers are intended to operate under unnormal conditions in order to clear the fault & to isolate the defective circuits protecting its associated electrical equipment, therefore breaking and making capacities are considered as the most important criteria as far Circuit breaker are concerned.
The making current is not an RMS value it is the peak value ie. Impk = 2.5Irms. The peak value of 2.5 times RMS is the DC offset at point when the LBS closes on the fault and is taken as the worst case X/R ratio of the source (X/R of about 20). This peak decays to RMS value Ith (thermal withstand current) dependent on the X/R delay constant. The decay rate is exponential with time. There is a misconception that making is 2.5times breaking current, but making is normally quoted as a peak and breaking as RMS. The breaking current in a CB is an RMS value. Breaking fault current is far more difficult that making especially when the contacts open when current is not at zero crossing point on the sine wave. For HV systems 132KV and above, the restrike and TRV starts to become a major consideration in CB selection, especially for long cables and lines.
- Breaking capacity.
- Making Capacity.
Making capacity is more higher since it is considering the initial starting current, inrush and faults that might occur at switching on moment.
Accordingly, the Circuit breakers have both while the Isolator or LBS has only breaking capacity. Isolator therefore used to isolate/disconnect/break load. To be switched on only under no load.
Basically and LBS is only designed to make and break load currents. It can be closed onto a fault (has a making rating) and cannot break a fault current. A CB is designed to make and break fault currents and off course load currents. Need to be careful with switching long cables and long lines with LBS, due to its limitation with switching cable/line charging (highly capacitive) currents. Similar precaution with needed with switching reactive loads like large transformers. Normally a CB is recommended for the 2 latter cases. Check the manufacturer test specs.
In simple way the Load Break Switch used to cut off healthy circuits or to break / disconnect the load. As a precaution, normally the LBS / Isolator are to be switched on under no load, the connected load to be utilized after switching on the Isolator. This why it has no making capacity. Circuit Breakers are intended to operate under unnormal conditions in order to clear the fault & to isolate the defective circuits protecting its associated electrical equipment, therefore breaking and making capacities are considered as the most important criteria as far Circuit breaker are concerned.
The making current is not an RMS value it is the peak value ie. Impk = 2.5Irms. The peak value of 2.5 times RMS is the DC offset at point when the LBS closes on the fault and is taken as the worst case X/R ratio of the source (X/R of about 20). This peak decays to RMS value Ith (thermal withstand current) dependent on the X/R delay constant. The decay rate is exponential with time. There is a misconception that making is 2.5times breaking current, but making is normally quoted as a peak and breaking as RMS. The breaking current in a CB is an RMS value. Breaking fault current is far more difficult that making especially when the contacts open when current is not at zero crossing point on the sine wave. For HV systems 132KV and above, the restrike and TRV starts to become a major consideration in CB selection, especially for long cables and lines.
You may also like:
The method of creating a die-cast rotor is as follows:
1. An assembly of steel laminations (which may or may not be grain-oriented) containing the openings for both rotor bars and ventilation (as required) is ...
For flyback & boost applications, powder cores such as Kool-mu, Xmu, etc... are usually best performing and lowest cost. Even these may need to be gapped and if CCM operation is required, a "stepped-gap" ...
When operating an AC machine on a variable frequency drive, the most common approach is to mimic the DC curves. This is done by using a constant volt/hertz ratio until a "base" speed is achieved at rated ...
The aforementioned types of Circuit Breakers are used in LV System and generally based on the same operating principle.
MCB and MCCB/ICCB have a bimetal heater for overload which releases the Contact s while ...
In inverter regular inspection, we must cut off power before operation. Wait 4minutes (the bigger the longer, the maximum waiting time is 15 minutes) till the frequency inverter display panel LED indicator ...
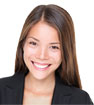
Featured
Like pumps, fans consume significant electrical energy while serving several applications. In many plants, the VFDs (variable ...
A frequency inverter controls AC motor speed. The frequency inverter converts the fixed supply frequency (60 Hz) to a ...
Motor starter (also known as soft starter, motor soft starter) is a electronic device integrates soft start, soft stop, ...
Soft starter allows the output voltage decreases gradually to achieve soft stop, in order to protect the equipment. Such as the ...
Soft Starter reduces electric motor starting current to 2-4 times during motor start up, reduces the impact to power grid during ...

In Discussion