Heavily discontinuous mode flyback design
With a heavily discontinuous mode flyback design, the transformer's ac portion of current can be larger than the dc portion. When a high perm material is used for the transformer core, the required gap can be quite large in order to reach the low composite permeability required while the core size will likely be driven by winding and core loss considerations rather than just simply avoiding saturation. Normally the gap is put in the center leg only (with E type topology cores) in order to minimize the generation of stray fields. However, in designs such as yours (high ac with a high perm core) the needed core gap can lead to a relatively large fringing zone through which foil or solid wire may not pass without incurring excessive, unacceptable loss. Possible solutions are to use Litz wire windings or inert spacers (e.g., tape) around the center leg in order to keep the windings far enough away from the gap (the rule of thumb is 3 to 5 gap lengths, which can eat up a lot of the window area).
It is mainly for these reasons that placing half the gap in an E type core's outer legs might be worth the trouble of dealing with the magnetic potential between the core halves (and you have seen first hand what trouble an ill designed shield band can be).
To avoid eddy current losses, the shield band should be spaced well away from the outer leg gap, probably 5 gap lengths or more. Also to be a really effective magnetic shield, it should be 3 to 5 gap lengths thick.
Bear in mind that with a high frequency, high ac current inductor design proximity effects in the winding may become very significant. This is why many of these type of inductors have single layer windings or winding wound with Litz wire (foil is the worst winding type here). One advantage of an equally gapped E type core design is that the proximity effect on the windings is significantly less because there are two gaps in series (a quasi distributed gapped core design). Not only layer-to-layer, but turn-to-turn proximity effects can sometimes be problematic in an ac inductor (or flyback) design. Just as with the gap, these are reduced by adding appropriate spacing, for example making the winding coil loose or winding it bifilar with a non-conductive filament.
It is mainly for these reasons that placing half the gap in an E type core's outer legs might be worth the trouble of dealing with the magnetic potential between the core halves (and you have seen first hand what trouble an ill designed shield band can be).
To avoid eddy current losses, the shield band should be spaced well away from the outer leg gap, probably 5 gap lengths or more. Also to be a really effective magnetic shield, it should be 3 to 5 gap lengths thick.
Bear in mind that with a high frequency, high ac current inductor design proximity effects in the winding may become very significant. This is why many of these type of inductors have single layer windings or winding wound with Litz wire (foil is the worst winding type here). One advantage of an equally gapped E type core design is that the proximity effect on the windings is significantly less because there are two gaps in series (a quasi distributed gapped core design). Not only layer-to-layer, but turn-to-turn proximity effects can sometimes be problematic in an ac inductor (or flyback) design. Just as with the gap, these are reduced by adding appropriate spacing, for example making the winding coil loose or winding it bifilar with a non-conductive filament.
You may also like:
The method of creating a die-cast rotor is as follows:
1. An assembly of steel laminations (which may or may not be grain-oriented) containing the openings for both rotor bars and ventilation (as required) is ...
There are two important different parameters as far as the disconnection/connection of Electrical utilities is concerned.
- Breaking capacity.
- Making Capacity.
It is not easily answered since there are many variables at play which will affect the starting time. For a large medium voltage motor, it is recommended that a motor starting analysis be performed so that ...
There are possibilities of having inter-turn faults on the rotor winding: when the insulation positioned between adjacent conductors break (electrically) over time under certain mechanisms. These mechanisms ...
For flyback & boost applications, powder cores such as Kool-mu, Xmu, etc... are usually best performing and lowest cost. Even these may need to be gapped and if CCM operation is required, a "stepped-gap" ...
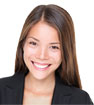
Featured
Like pumps, fans consume significant electrical energy while serving several applications. In many plants, the VFDs (variable ...
A frequency inverter controls AC motor speed. The frequency inverter converts the fixed supply frequency (60 Hz) to a ...
Motor starter (also known as soft starter, motor soft starter) is a electronic device integrates soft start, soft stop, ...
Soft starter allows the output voltage decreases gradually to achieve soft stop, in order to protect the equipment. Such as the ...
Soft Starter reduces electric motor starting current to 2-4 times during motor start up, reduces the impact to power grid during ...

In Discussion
Circuit Breaker Analyzer in Preventive Maintenance Plan
Solar Panel Made In America Requirements
Electrical distribution system
Connection of 24 relay
Time-domain analysis or frequency-response analysis
Agitated pressure filter dryer
Define "Power Electronics"
How would you code this in logic controller?
Solar Panel Made In America Requirements
Electrical distribution system
Connection of 24 relay
Time-domain analysis or frequency-response analysis
Agitated pressure filter dryer
Define "Power Electronics"
How would you code this in logic controller?