Home » Blog » Automation controls » Different brushes at same ring
Different brushes at same ring
Recently I had to do a report explain why is impossible join brushes, at same time, from different companies, even with same characteristics.
I used the follow points:
1 - Even with same characteristics the final results is different because tue proportion of material and/or manufacturing process different lead to a different brushes;
2 - Guarantee, because our machine is new, and is a good practice use brushes recommended by Manufacturer;
3 - The film, that is formed on the rings by the brushes could change (but I don't have any sure if chage for bad);
Unfortunately my report was based on experience for old engineer and recommendation of Manufacturer.
One of the most important thing about brushes in high current density environments is uniformity. If there are any variations in material composition, manufacturing methods, dimensions, porosity, density, surface hardness, friction coefficient, pig-tail attaching means, size of pig-tail conductor, etc., there will be a variation in the current division and/or wear.
Ultimately some brushes will carry more current than others and the increased current density in those brushes will lead to overheating, pitting, scoring, and ultimately costly repairs to the commutator/slip-rings. You might also accidentally mix brush grades when dealing with multiple vendors.
Although manufacturers publish data for brush materials which may prove to be very close to one another, mixing them on a collector surface is not a good practice. Any signs of undesirable performance would be difficult to identify the root cause for and small differences in electrical resistance can produce staggeringly varied performance from each brush.
While the materials used have good material data supplied with them, the manufacturing of the cable connection does not which can account for many times the resistivity differences of the material. Brush manufacturers do use a variety of materials here also and so some brushes, even of the same grade and from the same supplier but with different connection material, cannot be used together.
Mixing of grades is an uncontrolled practice which leads to variable surface conditions especially where the numbers of each grade used is not controlled.
Lower resistance brushes will "grab" the current possibly over filming the collector surface leaving the higher resistance brushes to run at lower than prescribed minimum current densities which results in higher coefficients of friction at the brush/collector interface. You would never know when your film is stable which endangers machine life.
Most machine manufacturers select a grade of carbon to use which is useful at the machines fully rated capacity. However, manufacturing tolerances, specifications etc can produce a machine vastly over rated for your application. Running the manufacturers supplied brushes at reduced load can be very damaging. Most Manufacturers will accept that you need another brush grade for your specific use and will maintain warranty provided they have been consulted regarding any changes.
Many overlook that by moving a machine from one position in their plant to another, that they well need to consider the brush grade at that time also. Sometimes a simple and cost effective reduction of brushes (of the same grade) within the machine can increase plant reliability and longevity dramatically. Other times a consultation with a brush expert can lead to an alternative grade to produce better performance.
I used the follow points:
1 - Even with same characteristics the final results is different because tue proportion of material and/or manufacturing process different lead to a different brushes;
2 - Guarantee, because our machine is new, and is a good practice use brushes recommended by Manufacturer;
3 - The film, that is formed on the rings by the brushes could change (but I don't have any sure if chage for bad);
Unfortunately my report was based on experience for old engineer and recommendation of Manufacturer.
One of the most important thing about brushes in high current density environments is uniformity. If there are any variations in material composition, manufacturing methods, dimensions, porosity, density, surface hardness, friction coefficient, pig-tail attaching means, size of pig-tail conductor, etc., there will be a variation in the current division and/or wear.
Ultimately some brushes will carry more current than others and the increased current density in those brushes will lead to overheating, pitting, scoring, and ultimately costly repairs to the commutator/slip-rings. You might also accidentally mix brush grades when dealing with multiple vendors.
Although manufacturers publish data for brush materials which may prove to be very close to one another, mixing them on a collector surface is not a good practice. Any signs of undesirable performance would be difficult to identify the root cause for and small differences in electrical resistance can produce staggeringly varied performance from each brush.
While the materials used have good material data supplied with them, the manufacturing of the cable connection does not which can account for many times the resistivity differences of the material. Brush manufacturers do use a variety of materials here also and so some brushes, even of the same grade and from the same supplier but with different connection material, cannot be used together.
Mixing of grades is an uncontrolled practice which leads to variable surface conditions especially where the numbers of each grade used is not controlled.
Lower resistance brushes will "grab" the current possibly over filming the collector surface leaving the higher resistance brushes to run at lower than prescribed minimum current densities which results in higher coefficients of friction at the brush/collector interface. You would never know when your film is stable which endangers machine life.
Most machine manufacturers select a grade of carbon to use which is useful at the machines fully rated capacity. However, manufacturing tolerances, specifications etc can produce a machine vastly over rated for your application. Running the manufacturers supplied brushes at reduced load can be very damaging. Most Manufacturers will accept that you need another brush grade for your specific use and will maintain warranty provided they have been consulted regarding any changes.
Many overlook that by moving a machine from one position in their plant to another, that they well need to consider the brush grade at that time also. Sometimes a simple and cost effective reduction of brushes (of the same grade) within the machine can increase plant reliability and longevity dramatically. Other times a consultation with a brush expert can lead to an alternative grade to produce better performance.
You may also like:
Using solar output distributed to offset the dirtiest, most expensive and most distribution grid loading power enhances and optimizes the value and worth of that solar generated power - both economically and ...
A lighting control panel will have mostly single-pole breakers with phase-to-neutral branch circuits feeding lighting circuitry. There is the added possibility of having either 'smart' breakers or integral ...
SCR's are limited to a maximum current rating, as well as a maximum voltage rating. In addition, the number of starts per hour is also limited. A combination of voltage spikes, too many starts per hour, or too ...
AC Motors - Variable torque: AC motors have a speed torque characteristic that varies as the square of the speed.
AC Motors - Constant torque: These ac motors can develop the same torque at each speed, thus ...
When conducting insulation testing, the most important consideration is consistency. Always test at the same location, use the same test voltage, perform the test for the same amount of time, and use the same ...
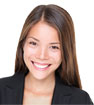
Featured
Like pumps, fans consume significant electrical energy while serving several applications. In many plants, the VFDs (variable ...
A frequency inverter controls AC motor speed. The frequency inverter converts the fixed supply frequency (60 Hz) to a ...
Motor starter (also known as soft starter, motor soft starter) is a electronic device integrates soft start, soft stop, ...
Soft starter allows the output voltage decreases gradually to achieve soft stop, in order to protect the equipment. Such as the ...
Soft Starter reduces electric motor starting current to 2-4 times during motor start up, reduces the impact to power grid during ...

In Discussion
HMI Concept development
Generate output as 4mA and takes as input 24 volts DC
Can we also use hard cable for battery termination in UPS?
Reasons for energy meter flashover?
OVP and Noisy Output Voltage problem with Single Stage LED Driver
Hipot testing of Electric Machines
Convert 3 phase motor into 1 phase motor?
Determine the effect of reduced power factor on the real power consumption
Generate output as 4mA and takes as input 24 volts DC
Can we also use hard cable for battery termination in UPS?
Reasons for energy meter flashover?
OVP and Noisy Output Voltage problem with Single Stage LED Driver
Hipot testing of Electric Machines
Convert 3 phase motor into 1 phase motor?
Determine the effect of reduced power factor on the real power consumption