I've seen some attempt of electrical driven prototypes in the field, but
is still not an enough big sector that let you find specific
literature. Excluding the large dumpers for mining, probably the only
machine that is built in series is D7E from CAT.
One of largest engineering challenge that you will face on a similar application, is the cooling to the power electronic. You can consider that you will have to dissipate 3-5% of the power that your driver is processing and the max temperature of IGBT's is not so far from the max temperature in that your vehicle can operate. A small temperature delta, mean a large heat exchanger and/or pretty high speed of air through it. (That with all the problems related to that). A possible solution is liquid cool the IGBT's mounting them on the aluminum plate. You can't use the engine cooling fluid because it too warm, but you may can use hydraulic oil (that should never get warmer of 55C).
One of largest engineering challenge that you will face on a similar application, is the cooling to the power electronic. You can consider that you will have to dissipate 3-5% of the power that your driver is processing and the max temperature of IGBT's is not so far from the max temperature in that your vehicle can operate. A small temperature delta, mean a large heat exchanger and/or pretty high speed of air through it. (That with all the problems related to that). A possible solution is liquid cool the IGBT's mounting them on the aluminum plate. You can't use the engine cooling fluid because it too warm, but you may can use hydraulic oil (that should never get warmer of 55C).
Modulating Supply & Return Fans are used as a means of providing proper variable air volume (VAV) control as well as building pressurization. Many such VAV systems are still largely pneumatic with static to the downstream boxes being maintained by inlet guide vanes. To provide increased energy savings and energy comfort, these systems can be easily converted to frequency inverter fan control of the supply and return fans and Direct Digital Control (DDC) to coordinate any increased energy saving strategies.
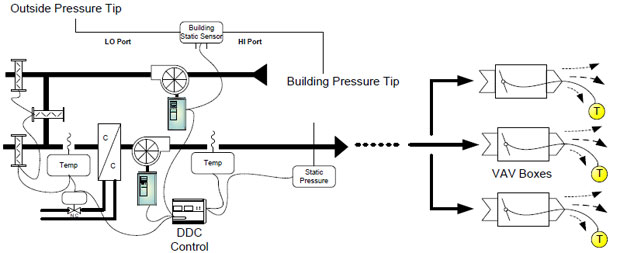
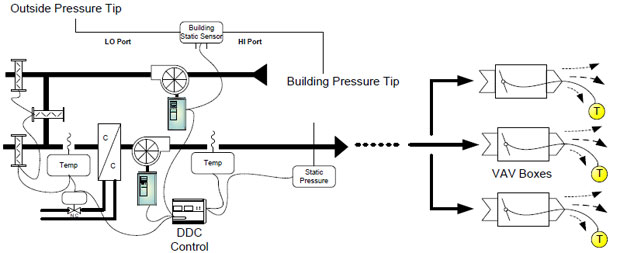
New improvements make a long list but one of the most recent is being able to switch a DB to and from optimised. How many times in previous versions did I forget to check the box then have to delete the DB and create it again. PID loop tuning function within TIA is useful and if you look on the Siemens Automation website (UK/Europe) the example files are growing all the time and they have some great examples that can be integrated easily in to application, I have used the ASi maintenance and monitoring example which was very well put together along with a few others. Even if you don't use them but need some pointers on which way to go they are a good starting point.
Unfortunately my report was based on experience for old engineer and recommendation of Manufacturer.
One of the most important thing about brushes in high current density environments is uniformity. If there are any variations in material composition, manufacturing methods, dimensions, porosity, density, surface hardness, friction coefficient, pig-tail attaching means, size of pig-tail conductor, etc., there will be a variation in the current division and/or wear.
Where we really need digital communication networking, in my personal opinion, is down at the sensor/transmitter and positioner/actuator/valve level to take the place of 4-20 mA and on/off signals. Down at the level 1 of the Purdue reference model you need a fieldbus, not one of the "H2" types of fieldbus, but one of the "H1" types of fieldbus. When first introduced, these technologies were not as fast and not as easy to use has they could have been, but after many years of refinement these technologies are finally becoming sufficiently easy for most plants to use.
How to make our systems so friendly that they do not need technicians to help diagnose problems? Most of the more obvious answers have been well documented here but to emphasize these points it is normally the case that diagnostics and alarms can dominate the amount of code constructed for an application.
Phase rotation errors are not as rare as they ought to be. I've seen more than one building with a systematic phase rotation error. This can be prevented by carefully following the color coding system (Yellow Orange Brown and Red Blue Black for 480 volt and 208 volt systems in the US for example) and tagging feeders at both ends to assure proper connections.
Variable frequency drives are important power electronic devices. When we start an electric motor, we are increasing from 0 speed to full operating speed. A VFD ensures that the motor accelerates (increases its speed) to its full speed in a smooth manner, without causing much irregularities. In other words, VFDs make the motor accelerate uniformly.
VFDs are also easy to install and use. VFD drives are not only for starting motors (like the normal starters), but for easy speed control as well.
I have a problem with ABB ACS800-104-0105-3 drive model, the output current reading on the VFD is always double the reading of the clamp ampere(i.e. drive reading= 40 A, clamp ampere reading=20 A), what is the procedure that i can follow to detect the cause of this error?
Transistor frequency inverter has the following disadvantages: easy trip, difficult re-start, poor overload capacity. As the rapid development of IGBT and CPU, the inverter drive integrates perfect self-diagnosis and fault prevention features, improve the reliability greatly.
Variable frequency drives are electronic devices, they have stringent requirements in installation environment which is specified in its user manual normally. In exceptional circumstances, if it does not meet these requirements, we must adopt appropriate suppression measures: vibration is the main reason to cause electronic devices mechanical damaged, for big shock and vibration occasions, we should use rubber anti-vibration measures.
Two electrical motors that design for altitude <1000 m but now this two electrical motor have installed on altitude 1880 m and this electrical motors become very hot. The electrical machines power is 15300KW & 9700KW and they cooled by force air and water cooler.
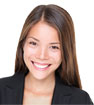
Featured
Like pumps, fans consume significant electrical energy while serving several applications. In many plants, the VFDs (variable ...
A frequency inverter controls AC motor speed. The frequency inverter converts the fixed supply frequency (60 Hz) to a ...
Motor starter (also known as soft starter, motor soft starter) is a electronic device integrates soft start, soft stop, ...
Soft starter allows the output voltage decreases gradually to achieve soft stop, in order to protect the equipment. Such as the ...
Soft Starter reduces electric motor starting current to 2-4 times during motor start up, reduces the impact to power grid during ...

In Discussion
Pumping in salty conditions
Calculating 30min annual maximum demand on the substation transformer.
What is the Difference Between SERVO Drives & VFD?
Feedre protection
"Green Economy" Wind, Solar, Green Building, Geothermal are growing
Classification of Hazardous Areas - Biodiesel Vacuum Distillation
how can we reduce the flash steam in condensate tank?
Flyback design
Calculating 30min annual maximum demand on the substation transformer.
What is the Difference Between SERVO Drives & VFD?
Feedre protection
"Green Economy" Wind, Solar, Green Building, Geothermal are growing
Classification of Hazardous Areas - Biodiesel Vacuum Distillation
how can we reduce the flash steam in condensate tank?
Flyback design