Home » Blog » Automation controls » Design a PMSM to 10000 rpm high speed
Design a PMSM to 10000 rpm high speed
Synchronous speeds are a function of the applied frequency and the number of poles, governed by the equation
120 * (frequency in hertz) / (poles) = (speed in rpm).
Adjust the ratio of frequency to poles to achieve the desired speed.
(example: a 4-pole design would require a line frequency of 333.33 Hz ... which means operating on either an adjustable speed drive or on a dedicated high-frequency power system.)
Once you've got the electro-magnetics sorted out, it's a matter of manufacturing to the mechanical constraints associated with the rotational speed.
Well, depending on the power rating, and on the required reliability, I believe it's very simply. The biggest problem would be to get a variable frequency drive, or other power supply to provide a 3-phase output frequency of about 500Hz.
An automotive alternator should be able to operate relatively reliably at your required speed, and it can probably deliver around 1.5kW at that speed.
In order to make it permanently magnetised, we just have to disassemble the rotor, take the rotor windings out, and replace them with some ring-shaped permanent magnet. We may possibly also use a number of individual smaller permanent magnets embedded in some non-magnetic material such a copper or aluminium between the two half-shelves of the rotor. Depending on the construction of the alternator, we may need some machine shop to pull the rotor halves apart, perhaps machine some material away to make room for the permanent magnet(s), and to press the assembly back together again, and to balance it afterwards.
120 * (frequency in hertz) / (poles) = (speed in rpm).
Adjust the ratio of frequency to poles to achieve the desired speed.
(example: a 4-pole design would require a line frequency of 333.33 Hz ... which means operating on either an adjustable speed drive or on a dedicated high-frequency power system.)
Once you've got the electro-magnetics sorted out, it's a matter of manufacturing to the mechanical constraints associated with the rotational speed.
Well, depending on the power rating, and on the required reliability, I believe it's very simply. The biggest problem would be to get a variable frequency drive, or other power supply to provide a 3-phase output frequency of about 500Hz.
An automotive alternator should be able to operate relatively reliably at your required speed, and it can probably deliver around 1.5kW at that speed.
In order to make it permanently magnetised, we just have to disassemble the rotor, take the rotor windings out, and replace them with some ring-shaped permanent magnet. We may possibly also use a number of individual smaller permanent magnets embedded in some non-magnetic material such a copper or aluminium between the two half-shelves of the rotor. Depending on the construction of the alternator, we may need some machine shop to pull the rotor halves apart, perhaps machine some material away to make room for the permanent magnet(s), and to press the assembly back together again, and to balance it afterwards.
You may also like:
I remember my very first power supply. They threw me in the deep end in 1981 building a multi-output 1 kW power supply. I was fresh from college, thought i knew everything, and consumed publications ...
1. Voltage unbalance in supply side (1% volts could easily be 10% current).
2. Physical differences between individual stator coil shapes and connections causing small (but noticeable) resistance changes. ...
The high frequency edges of switched waveforms can cause capacitively coupled currents to flow from windings to frame, returning through the bearings, and these can accelerate corrosion in the bearings, ...
Variable speed drive switches very fast which brings high dv/dt on motor. How often do we face with problems coming with VSD? How harmful is the common mode currents in windings and other parts of motor due to ...
For a "physical" interpretation, reactive current (power/KVA flow), in my opinion is best looked at from the perspective of a generator connected directly to an infinite bus (in LV generators this is the norm).
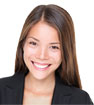
Featured
Like pumps, fans consume significant electrical energy while serving several applications. In many plants, the VFDs (variable ...
A frequency inverter controls AC motor speed. The frequency inverter converts the fixed supply frequency (60 Hz) to a ...
Motor starter (also known as soft starter, motor soft starter) is a electronic device integrates soft start, soft stop, ...
Soft starter allows the output voltage decreases gradually to achieve soft stop, in order to protect the equipment. Such as the ...
Soft Starter reduces electric motor starting current to 2-4 times during motor start up, reduces the impact to power grid during ...

In Discussion
Looking for 4 Mw PV modules 250Wp poly EU production
What's the alternative for a solar system?
400 kV transmission line charging
In case Copper, annealed soft-drawn...
Design Implications in Sub Micron Positioning
What are 3 of the biggest risks when investing in PV energy?
Controlling exotherm in a batch reactor using cooling water
Rated and Normal pump flow
What's the alternative for a solar system?
400 kV transmission line charging
In case Copper, annealed soft-drawn...
Design Implications in Sub Micron Positioning
What are 3 of the biggest risks when investing in PV energy?
Controlling exotherm in a batch reactor using cooling water
Rated and Normal pump flow