Home » Blog » Automation controls » Compensate electric motors effect of high altitude
Compensate electric motors effect of high altitude
Case: Two electrical motors that design for altitude <1000 m but now this two electrical motor have installed on altitude 1880 m and this electrical motors become very hot. The electrical machines power is 15300KW & 9700KW and they cooled by force air and water cooler.
First - machines designed for higher-than-normal altitude (i.e. in excess of 1000 m = 3300 ft above sea level) are designed with lower allowable temperature rises. The rule-of-thumb approximation is 1 degree C for every 100 m above 1000.
This means a typical Class B rise (max 80 C over 40 C ambient) will be designed for a max 71 C rise over ambient at 1880 m altitude.
Since temperature is more-or-less proportional to the square of the current, the design either reduced in output power to limit the current, or is "overdesigned" so that the resultant output power is the effective de-rate condition. In this case, the "sea level" rating of 15300 kW would become 15300 * (71/80)^2 = 15300 * 0.94 = 14382 kW. Likewise, the 9700 kW machine would be rated for 9118 kW.
The ability to cool the machine effectively is based on two things: the amount of coolant in direct contact with the heat source(s), and the pressure of the coolant flow. At altitude, the density of the coolant is reduced significantly, hence the requirement to operate at lower power ratings. The pressure of the airflow over the windings, etc is ALSO reduced at higher altitude, making the cooling more inefficient.
Speeding up the blower (i.e. going from 6 pole speed to 4 pole speed, for example) will overcome some of this by increasing both airflow and pressure. However, the power draw on the blower drive motor may also necessitate an increase in size to accommodate the new loading parameters (including the effects of high altitude on it!). Note that if the air movement within the machine enclosure is dependent solely on the MACHINE rotor speed (i.e. a shaft mounted fan), there will be a need to develop and apply a separately-powered fan to accommodate the required changes.
The probability of voltage breakdown / corona / flashover is increased above 1800 m as well, which means at least taking a cursory look at both creepage and strike distances.
And finally - if, after all this, the machine is still overheating ... time to look at the cleanliness of the liquid side of the heat exchanger. This may mean cleaning or replacing the tubing and headers, determining liquid flow rates (and pressures) and ensuring they are within original design criteria (roughly 3.8 litres per minute for each kW of loss in the rotating machine).
First - machines designed for higher-than-normal altitude (i.e. in excess of 1000 m = 3300 ft above sea level) are designed with lower allowable temperature rises. The rule-of-thumb approximation is 1 degree C for every 100 m above 1000.
This means a typical Class B rise (max 80 C over 40 C ambient) will be designed for a max 71 C rise over ambient at 1880 m altitude.
Since temperature is more-or-less proportional to the square of the current, the design either reduced in output power to limit the current, or is "overdesigned" so that the resultant output power is the effective de-rate condition. In this case, the "sea level" rating of 15300 kW would become 15300 * (71/80)^2 = 15300 * 0.94 = 14382 kW. Likewise, the 9700 kW machine would be rated for 9118 kW.
The ability to cool the machine effectively is based on two things: the amount of coolant in direct contact with the heat source(s), and the pressure of the coolant flow. At altitude, the density of the coolant is reduced significantly, hence the requirement to operate at lower power ratings. The pressure of the airflow over the windings, etc is ALSO reduced at higher altitude, making the cooling more inefficient.
Speeding up the blower (i.e. going from 6 pole speed to 4 pole speed, for example) will overcome some of this by increasing both airflow and pressure. However, the power draw on the blower drive motor may also necessitate an increase in size to accommodate the new loading parameters (including the effects of high altitude on it!). Note that if the air movement within the machine enclosure is dependent solely on the MACHINE rotor speed (i.e. a shaft mounted fan), there will be a need to develop and apply a separately-powered fan to accommodate the required changes.
The probability of voltage breakdown / corona / flashover is increased above 1800 m as well, which means at least taking a cursory look at both creepage and strike distances.
And finally - if, after all this, the machine is still overheating ... time to look at the cleanliness of the liquid side of the heat exchanger. This may mean cleaning or replacing the tubing and headers, determining liquid flow rates (and pressures) and ensuring they are within original design criteria (roughly 3.8 litres per minute for each kW of loss in the rotating machine).
You may also like:
The key to optimizing the system operation is communication and information sharing through the entire system equipment. With the reduced cost of variable frequency drives and Building Automation Systems, ...
Due to variable frequency drive can adapt to various requirements in production process, especially in the industrial automation control applications, AC variable frequency control technology has risen to be ...
If you are interested in power electronics design at the board or system level, I would recommend LTspice (note the correct spelling) by far above all the others. In addition to being superb for IC design ...
Determination of required grounding impedance is based on determination of coefficient of grounding which represents ratio of maximum phase voltage at phases which aren't exposed by fault and line voltage of ...
AC Motors - Variable torque: AC motors have a speed torque characteristic that varies as the square of the speed.
AC Motors - Constant torque: These ac motors can develop the same torque at each speed, thus ...
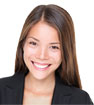
Featured
Like pumps, fans consume significant electrical energy while serving several applications. In many plants, the VFDs (variable ...
A frequency inverter controls AC motor speed. The frequency inverter converts the fixed supply frequency (60 Hz) to a ...
Motor starter (also known as soft starter, motor soft starter) is a electronic device integrates soft start, soft stop, ...
Soft starter allows the output voltage decreases gradually to achieve soft stop, in order to protect the equipment. Such as the ...
Soft Starter reduces electric motor starting current to 2-4 times during motor start up, reduces the impact to power grid during ...

In Discussion
Advantages/Disadvantages of String inverters vs. Central inverters?
Insulation Resistance of generator stator drops
Vibration in Vertical Pumps
Simulation and Modelling, who uses it, and for what?
What is the relationship between inducer and NPSH?
General purpose software tool for designing multiple output flyback converters
How to select a breaker??
VFD used as main power supply question
Insulation Resistance of generator stator drops
Vibration in Vertical Pumps
Simulation and Modelling, who uses it, and for what?
What is the relationship between inducer and NPSH?
General purpose software tool for designing multiple output flyback converters
How to select a breaker??
VFD used as main power supply question