Choose motors for electric vehicles
My experience with the types of motors in electric vehicle is the following. There are three choices for motors in EVs, permanent magnet PM, integral permanent magnet IPM, and induction motor IM. They each have their pros and cons. A PM has the highest power density; it was used on a military HEV on which I worked. A con for the PM is the back emf during a vehicle run-away. If the vehicle were to go down hill at a high rate of speed a large bemf would be generated that would damage the IGBTs due to excessive DC bus voltage. The integral permanent magnet motor has smaller power density because the magnets are smaller and interior to the rotor, but is a compromise on the excessive bemf during a run away. The IPM has "half" permanent magnet torque and "half" reluctance torque. The IM has the smallest power density, and thus the physically largest for the same power and torque. On the other hand, it does not have an excessive bemf condition during run-away. The IM is also less expensive, but this was not the main consideration on the HEV on which I worked.
The major reason for using PM or IPM motors is power density and efficiency. That results in better mileage, lower weight and additionally less cooling required.
The cost for PM is significantly higher and availability is lower. Especially in Hybrids PM seems to be standard (e.g. Prius) but they have their own motor design.
For run-away the solution Chip suggested is an option. The short circuit currents are not necessary to high for the inverter if the inductance is high enough. That obviously needs a special design for the motor and possibly a short circuit device between motor and drive. Additionally the transients for the short circuit currents can be twice as high as the steady state short circuit currents. Another option would be to disconnect the driveline from the motor mechanically.
Another motor type that has not been discussed here is the high speed switched reluctance motor. Inexpensive to build and high efficiency (although lower power density).
The major reason for using PM or IPM motors is power density and efficiency. That results in better mileage, lower weight and additionally less cooling required.
The cost for PM is significantly higher and availability is lower. Especially in Hybrids PM seems to be standard (e.g. Prius) but they have their own motor design.
For run-away the solution Chip suggested is an option. The short circuit currents are not necessary to high for the inverter if the inductance is high enough. That obviously needs a special design for the motor and possibly a short circuit device between motor and drive. Additionally the transients for the short circuit currents can be twice as high as the steady state short circuit currents. Another option would be to disconnect the driveline from the motor mechanically.
Another motor type that has not been discussed here is the high speed switched reluctance motor. Inexpensive to build and high efficiency (although lower power density).
You may also like:
For small circuit breakers we can do the test of Magnetic protection behavior by using "Injection Current Apparatus", and suppose the CB's results were good, do you think it's enough? I'm sure not, because by ...
The surge impedance loading (SIL) of a line is the power load at which the net reactive power is zero. So, if your transmission line wants to "absorb" reactive power, the SIL is the amount of reactive power ...
r/min: motor rotation speed unit, the number of revolutions per minute, also can be expressed in rpm.
For example: 2-pole motor 50Hz 3000 r/min, 4-pole motor 50Hz 1500 r/min
Conclusion: The motor rotation ...
The biggest differences between the floor programmer and the office programmer is often a piece of paper (knowledge and experience do not replace a piece of paper in the mind of HR person that has no ...
I am currently investigating the design of a three phase axial flux PM motor, but replacing conventional materials with high temperature superconductors. I'm interested to know the thoughts of group members ...
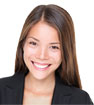
Featured
Like pumps, fans consume significant electrical energy while serving several applications. In many plants, the VFDs (variable ...
A frequency inverter controls AC motor speed. The frequency inverter converts the fixed supply frequency (60 Hz) to a ...
Motor starter (also known as soft starter, motor soft starter) is a electronic device integrates soft start, soft stop, ...
Soft starter allows the output voltage decreases gradually to achieve soft stop, in order to protect the equipment. Such as the ...
Soft Starter reduces electric motor starting current to 2-4 times during motor start up, reduces the impact to power grid during ...

In Discussion
SMPS with front end PFC in parallel
HT board tripping ckt
Currents in Y Phase connected to motor.
How and why eddy currents are formed in generators?
Sludge and Sediment Problem in Transformer
Reduce the cost of solar panels
Remedial Action Schemes or Special Protection Schemes
Everyone says or knows NPSHA should be greater then NPSHR
HT board tripping ckt
Currents in Y Phase connected to motor.
How and why eddy currents are formed in generators?
Sludge and Sediment Problem in Transformer
Reduce the cost of solar panels
Remedial Action Schemes or Special Protection Schemes
Everyone says or knows NPSHA should be greater then NPSHR