Cable length between VFD and Motor
The dU/dt at the output of the variable frequency drive combined with the motor cable length will result in very high voltage peaks at the motor terminals. This is a concern for the isolation in motors not designed to be driven by VFDs.
On the other hand the maximum motor cable length depends also on the switching frequency used due to the charging effect of the motor cable capacitance (this is a limitation on the variable frequency drive side, not on the motor isolation).
The dU/dt at motor terminals normally is very different from the dU/dt that you can calculate from IGBT and its driving characteristics (turn on time, gate resistor, etc) at variable frequency drive terminals. As the cable acts like a distributed LC impedance, the dU/dt calculation on VFD terminals will give you very high values that can be apparently dangerous, but in practice, will not happen at motor terminals.
For long cables, the combination of cable impedance, high frequency input impedance of motor and VFD switching frequency can lead to reflection of voltage pulses that gives origin to large voltage overshoots on motor terminals. The problem increases as increasing switching frequency because the time between voltage pulses will be smaller, so, a voltage pulse reaching the motor will add to the pulse being reflected. This “double pulsing” can results in extreme voltage overshoot and dU/dt that will result in motor insulation failures. For the variable frequency drives side the increasing switching frequency will be a problem (besides power losses) if you have a big capacitor filter at converter output, that can lead to high current pulses at inverter side.
The determination of the resulting dU/dt at motor terminals from the dU/dt at VFD drive terminals is very difficult if you try to use simulations. For this task you’ll need the high frequency parameters of cables (that also depends on installation details) and motor, that will not be available from standard datasheets and are very difficult to obtain from measurements. In practice almost all VFD manufacturers make extensive measurements and establish some criteria in order to orient applications. The approach is to determine if it is necessary or not to have an output filter for a known application (cable length).
For instance, a common specification is:
For cable lengths up to 100 meters (and motor suitable for variable frequency drive applications) it is not necessary a filter; for lengths from 100 to 200 meters, a series reactance can be used; for greater lengths it is necessary an LC filter at VFD terminals. The limit lengths can be different from different manufacturers and voltage levels (LV/MV). Gozuk, for instance, can give complete orientation for application of its drives considering the needed cable length for the application.
On the other hand the maximum motor cable length depends also on the switching frequency used due to the charging effect of the motor cable capacitance (this is a limitation on the variable frequency drive side, not on the motor isolation).
The dU/dt at motor terminals normally is very different from the dU/dt that you can calculate from IGBT and its driving characteristics (turn on time, gate resistor, etc) at variable frequency drive terminals. As the cable acts like a distributed LC impedance, the dU/dt calculation on VFD terminals will give you very high values that can be apparently dangerous, but in practice, will not happen at motor terminals.
For long cables, the combination of cable impedance, high frequency input impedance of motor and VFD switching frequency can lead to reflection of voltage pulses that gives origin to large voltage overshoots on motor terminals. The problem increases as increasing switching frequency because the time between voltage pulses will be smaller, so, a voltage pulse reaching the motor will add to the pulse being reflected. This “double pulsing” can results in extreme voltage overshoot and dU/dt that will result in motor insulation failures. For the variable frequency drives side the increasing switching frequency will be a problem (besides power losses) if you have a big capacitor filter at converter output, that can lead to high current pulses at inverter side.
The determination of the resulting dU/dt at motor terminals from the dU/dt at VFD drive terminals is very difficult if you try to use simulations. For this task you’ll need the high frequency parameters of cables (that also depends on installation details) and motor, that will not be available from standard datasheets and are very difficult to obtain from measurements. In practice almost all VFD manufacturers make extensive measurements and establish some criteria in order to orient applications. The approach is to determine if it is necessary or not to have an output filter for a known application (cable length).
For instance, a common specification is:
For cable lengths up to 100 meters (and motor suitable for variable frequency drive applications) it is not necessary a filter; for lengths from 100 to 200 meters, a series reactance can be used; for greater lengths it is necessary an LC filter at VFD terminals. The limit lengths can be different from different manufacturers and voltage levels (LV/MV). Gozuk, for instance, can give complete orientation for application of its drives considering the needed cable length for the application.
You may also like:
The basic configuration of a variable frequency drive is as follows.
Fig. 1 Basic configuration of variable frequency drive
Each part of a variable frequency drive has the following ...
I am trying to develop a controller for switched reluctance motor which minimizes torque ripple. My design is acquiring torque ripple information from speed signal. In simulation a high pass filter for speed ...
You already know from your engineering that higher voltages results to less operational losses for the same amount of power delivered. The bulk capacity of 3000MW has a great influence on the investment costs ...
For a DC Motor Armature, There is a simple method of determining the condition of the Armature.
Drop Test Method: Give a DC Voltage across the commutator Segments for one pole pitch area from a Power supply ...
There are two types of reactive consumptions in AC power system, inductive and capacitive reactances. We can not call them losses. The loss of a transmission line is the active power consumed by the line ...
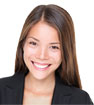
Featured
Like pumps, fans consume significant electrical energy while serving several applications. In many plants, the VFDs (variable ...
A frequency inverter controls AC motor speed. The frequency inverter converts the fixed supply frequency (60 Hz) to a ...
Motor starter (also known as soft starter, motor soft starter) is a electronic device integrates soft start, soft stop, ...
Soft starter allows the output voltage decreases gradually to achieve soft stop, in order to protect the equipment. Such as the ...
Soft Starter reduces electric motor starting current to 2-4 times during motor start up, reduces the impact to power grid during ...

In Discussion
Inrush current in transformer
The best option to separate a mixture of MEG and Crude oil?
Is anyone aware of a very small single phase pump that is listed
Chinese company is not protected by sales contract
Multiple Output Flyback Converter
Change motor star to delta connection
What is the most cost effective way of cutting lamination
Would rest of the world will survive for solar jobs in Solar industry?
The best option to separate a mixture of MEG and Crude oil?
Is anyone aware of a very small single phase pump that is listed
Chinese company is not protected by sales contract
Multiple Output Flyback Converter
Change motor star to delta connection
What is the most cost effective way of cutting lamination
Would rest of the world will survive for solar jobs in Solar industry?