Active power losses in electrical motor
Equivalent active power losses during electrical motor's testing in no-load conditions contain next losses:
1. active power losses in the copper of stator's winding which are in direct relation with square of no-load current value: Pcus=3*Rs*I0s*I0s,
2. active power losses in ferromagnetic core which are in direct relation with frequency and degree of magnetic induction (which depends of voltage):
a) active power losses caused by eddy currents: Pec=kec*f*(B)x
b) active power losses caused by hysteresis: Ph=(kh*d*d*f*f*B*B)/ρ
3. mechanical power losses which are in direct relation with square of angular speed value: Pmech=Kmech*ωmech*ωmech,
Comment:
First, as you can see, active power losses in ferromagnetic core of electrical motor depend of voltage value and frequency, so by increasing voltage value you will get higher active power losses in ferromagnetic core of electrical motor.
Second, you can't compare two electrical motors with different rated voltage and different rated power because active power losses in the ferromagnetic core, as I have already said above, depend of voltage value and frequency while active power losses in the copper of stator's windings depend of square of no-load current value which is different for electrical motors with different rated power.
Third, when you want to compare active power losses in no-load conditions of two electrical motors with same rated voltage and rated power, you need to check design of both electrical motors because it is possible that one of them has different kind of winding, because, maybe in the past, one of them was damaged, so its windings had to be changed, what could be the reason for different electrical design and that has a consequence different no-load current value.
1. active power losses in the copper of stator's winding which are in direct relation with square of no-load current value: Pcus=3*Rs*I0s*I0s,
2. active power losses in ferromagnetic core which are in direct relation with frequency and degree of magnetic induction (which depends of voltage):
a) active power losses caused by eddy currents: Pec=kec*f*(B)x
b) active power losses caused by hysteresis: Ph=(kh*d*d*f*f*B*B)/ρ
3. mechanical power losses which are in direct relation with square of angular speed value: Pmech=Kmech*ωmech*ωmech,
Comment:
First, as you can see, active power losses in ferromagnetic core of electrical motor depend of voltage value and frequency, so by increasing voltage value you will get higher active power losses in ferromagnetic core of electrical motor.
Second, you can't compare two electrical motors with different rated voltage and different rated power because active power losses in the ferromagnetic core, as I have already said above, depend of voltage value and frequency while active power losses in the copper of stator's windings depend of square of no-load current value which is different for electrical motors with different rated power.
Third, when you want to compare active power losses in no-load conditions of two electrical motors with same rated voltage and rated power, you need to check design of both electrical motors because it is possible that one of them has different kind of winding, because, maybe in the past, one of them was damaged, so its windings had to be changed, what could be the reason for different electrical design and that has a consequence different no-load current value.
You may also like:
Had run into a very serious field failure issue a decade ago due to IXYS FETs used in a phase-shifted ZVS bridge topology. Eventually, the problem was tracked to failure of the FETs' body diode when the unit ...
Paralleling IGBT modules where the IGBT but not the diode has a PTC is commonly done at higher powers. I personally have never done more than 3 x 600A modules in parallel but if you look at things like high ...
Modulating Supply & Return Fans are used as a means of providing proper variable air volume (VAV) control as well as building pressurization. Many such VAV systems are still largely pneumatic with static ...
Humidity plays important part in flashover. We faced a problem of flashovers in Air insulated 11kV Switchgear busbar compartments in rainy seasons. Any sharp edge will ionize the surrounding air, which becomes ...
For now I am working on a mining project which involves starting two SAG mills, the method of starting these mills is by rotor resistance and likewise we are using an energy recovery system (SER), could ...
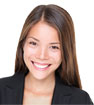
Featured
Like pumps, fans consume significant electrical energy while serving several applications. In many plants, the VFDs (variable ...
A frequency inverter controls AC motor speed. The frequency inverter converts the fixed supply frequency (60 Hz) to a ...
Motor starter (also known as soft starter, motor soft starter) is a electronic device integrates soft start, soft stop, ...
Soft starter allows the output voltage decreases gradually to achieve soft stop, in order to protect the equipment. Such as the ...
Soft Starter reduces electric motor starting current to 2-4 times during motor start up, reduces the impact to power grid during ...

In Discussion
How do you see the future of the solar market
What software would you suggest for design of BLDC motors?
Transformer for HF Series Resonant Inverter
Will altitude of 3000m be of any problem for insulated 11kV ABC cable?
What could be the main cause of the earth neutral voltage to be high
Cable Jointing
Power Supply Architecture 400 W Manager's Choice
Quick question: South facing roof
What software would you suggest for design of BLDC motors?
Transformer for HF Series Resonant Inverter
Will altitude of 3000m be of any problem for insulated 11kV ABC cable?
What could be the main cause of the earth neutral voltage to be high
Cable Jointing
Power Supply Architecture 400 W Manager's Choice
Quick question: South facing roof