Home » Blog » Automation controls » ACS800-104-0105-3 (ABB VFD Drives)
ACS800-104-0105-3 (ABB VFD Drives)
Question:
I have a problem with ABB ACS800-104-0105-3 drive model, the output current reading on the VFD is always double the reading of the clamp ampere(i.e. drive reading= 40 A, clamp ampere reading=20 A), what is the procedure that i can follow to detect the cause of this error?
Answer:
I don't know about ABB drives, but hope this thing will help you.
1. The variable frequency drive may have problem with current sensor, just replace with another drive for comparison.
2. Make sure you use, true RMS type clamp meter.
3. If there is leakage current (through cable insulation and air) between each phase. This normally because of the cable insulation already degraded. Add output reactor and replace the cable with suitable insulation can fix this kind of problem.
4. If there is leakage current between this VFD drive and the other drives, that both motor cable is quiet long and run in parallel together.
To Collect more data and get more idea, you can do this:
1. Clamp all the 3 phase motor cable together using clamp. The reading will show you the leakage current. Normally about 10% of motor rated current at full load.
2. Check the current on each phase, and see if the current is balance for each phase.
3. Run the variable frequency drive without the motor cable, check the current reading and clamp meter.
4. Run the AC drive with the motor cable but without the motor, check again the reading and clamp meter.
5. Run the drive with motor, check if any oscillation in motor current.
6. Check current input to the AC drive inverter.
7. Turn of the other drive (if the motor cable run parallel together with other VFDs), and see if any change in current.
I have a problem with ABB ACS800-104-0105-3 drive model, the output current reading on the VFD is always double the reading of the clamp ampere(i.e. drive reading= 40 A, clamp ampere reading=20 A), what is the procedure that i can follow to detect the cause of this error?
Answer:
I don't know about ABB drives, but hope this thing will help you.
1. The variable frequency drive may have problem with current sensor, just replace with another drive for comparison.
2. Make sure you use, true RMS type clamp meter.
3. If there is leakage current (through cable insulation and air) between each phase. This normally because of the cable insulation already degraded. Add output reactor and replace the cable with suitable insulation can fix this kind of problem.
4. If there is leakage current between this VFD drive and the other drives, that both motor cable is quiet long and run in parallel together.
To Collect more data and get more idea, you can do this:
1. Clamp all the 3 phase motor cable together using clamp. The reading will show you the leakage current. Normally about 10% of motor rated current at full load.
2. Check the current on each phase, and see if the current is balance for each phase.
3. Run the variable frequency drive without the motor cable, check the current reading and clamp meter.
4. Run the AC drive with the motor cable but without the motor, check again the reading and clamp meter.
5. Run the drive with motor, check if any oscillation in motor current.
6. Check current input to the AC drive inverter.
7. Turn of the other drive (if the motor cable run parallel together with other VFDs), and see if any change in current.
You may also like:
The transformer core can saturate due to, High Voltage, Low Frequency or a combination of both. Protection element V/Hz (ANSI 24) can be used to protect the transformer against over excitation as this can ...
In speaking with many engineers over several decades, a large manufacture of large electric motors, have decided once a rotor is identified as the problem, rebarring, or any single repair is usually ...
The second category, the motor design software, is specifically designed for motor analysis. It can be magnetic circuit based such as SPEED and RMXprt or full finite element based such as MotorSolve. The ...
Quality frequency inverters incorporate either an AC Reactor or DC Reactor (choke). Their inclusion in the basic design of the frequency inverter allows the design engineer to maximize the advantages of the ...
1: Torque boost: this function is the variable speed drive increases output voltage (mainly in low frequency) to compensate the torque loss due to voltage drop in the stator resistance, thereby improving the ...
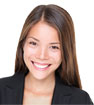
Featured
Like pumps, fans consume significant electrical energy while serving several applications. In many plants, the VFDs (variable ...
A frequency inverter controls AC motor speed. The frequency inverter converts the fixed supply frequency (60 Hz) to a ...
Motor starter (also known as soft starter, motor soft starter) is a electronic device integrates soft start, soft stop, ...
Soft starter allows the output voltage decreases gradually to achieve soft stop, in order to protect the equipment. Such as the ...
Soft Starter reduces electric motor starting current to 2-4 times during motor start up, reduces the impact to power grid during ...

In Discussion
PID control in DCS systems
Cu320-2 PN
Recommendations for Motion Control Industry Marketing and Sales
Can the rotor resistance drop down from its design value?
One cycle control for PFC or general DC/DC?
Rewind an Existing motor rating 400 hp-3.3 kv, 4 pole
queries regarding setting up solar power plant
Shading Effect
Cu320-2 PN
Recommendations for Motion Control Industry Marketing and Sales
Can the rotor resistance drop down from its design value?
One cycle control for PFC or general DC/DC?
Rewind an Existing motor rating 400 hp-3.3 kv, 4 pole
queries regarding setting up solar power plant
Shading Effect