Home » Blog » Experience » The cause of harmonics in variable frequency drive
The cause of harmonics in variable frequency drive
Before you attempt to dissipate causative factors of harmonics verbally, you take a look at several studies done by NEMA regarding such, and look into variable frequency drive (VFD) a bit better. You can view articles and studies by subscribing to the NEMA newsletter, and find other sources quite readily through NEMA. It's an easily accessible place for many current dissertations on this and other electrical topics, with excellent subject matter.
Categorizing all VFDs into the same bucket doesn't get it. You can also look at EPRI reports done better than 15 years ago on this and other VFD oriented subjects. Of course, all VFDs use Pulse Width Modulation to create the AC type wave form output (AKA 'Sinusoidal Flows) and of course all have rectifiers at the top end, as do all computers, PLCs, and many solid state control components. The differences of transient creation on the outputs of variable frequency drives depend upon the quality of the wave form output. The more transients or 'spikes' in the wave form, the more disruption potential. The quality of outputs of variable frequency drives can clearly be seen in testing with oscilloscopes. Several VFDs on the market significantly reduce this effect with chokes up front, and on the output. It really is a garbage in/garbage out situation that lesser drives don't bother to address.
Anytime AC is rectified to DC a field is created, and this is at best an elementary statement. The solution is good grounding to bleed it off. It isn't a problem to do so as long as the grounding pathway is adequate, a simple and proven fix. All drives employ capacitors. Motor field generation, field collapse of any wound coil has the potential of creating conductive/inductive reactance, and capacitors create capacitive reactance. To claim otherwise flies in the face of electrical fact. Phase balancing capacitor banks serve to bring about the same effect. As far as 'putting drives on a pedestal', you seem far more inclined to pursue a defensive posture than to take a better look at the correlation between capacitive and inductive/conductive reactance. Again, when these two factors meet the same frequency is when the distortion issue is brought to a peak, with these harmonics becoming the face of disruption.
I successfully remedied these situations by working with engineers in DOD and DOE facilities, as well as with a host of different independent companies, Gozuk, General Electric, Shaw Nuclear, being a few among them.
Categorizing all VFDs into the same bucket doesn't get it. You can also look at EPRI reports done better than 15 years ago on this and other VFD oriented subjects. Of course, all VFDs use Pulse Width Modulation to create the AC type wave form output (AKA 'Sinusoidal Flows) and of course all have rectifiers at the top end, as do all computers, PLCs, and many solid state control components. The differences of transient creation on the outputs of variable frequency drives depend upon the quality of the wave form output. The more transients or 'spikes' in the wave form, the more disruption potential. The quality of outputs of variable frequency drives can clearly be seen in testing with oscilloscopes. Several VFDs on the market significantly reduce this effect with chokes up front, and on the output. It really is a garbage in/garbage out situation that lesser drives don't bother to address.
Anytime AC is rectified to DC a field is created, and this is at best an elementary statement. The solution is good grounding to bleed it off. It isn't a problem to do so as long as the grounding pathway is adequate, a simple and proven fix. All drives employ capacitors. Motor field generation, field collapse of any wound coil has the potential of creating conductive/inductive reactance, and capacitors create capacitive reactance. To claim otherwise flies in the face of electrical fact. Phase balancing capacitor banks serve to bring about the same effect. As far as 'putting drives on a pedestal', you seem far more inclined to pursue a defensive posture than to take a better look at the correlation between capacitive and inductive/conductive reactance. Again, when these two factors meet the same frequency is when the distortion issue is brought to a peak, with these harmonics becoming the face of disruption.
I successfully remedied these situations by working with engineers in DOD and DOE facilities, as well as with a host of different independent companies, Gozuk, General Electric, Shaw Nuclear, being a few among them.
How do I configure my VFD in order to stop it from making so much noise? I use a GK 3000 for a 15 kw 50hz siemens motor. I must work at 1000 rpm. Noise is really disturbing, above 100 db. I have tried with another inverter and found that the cause of the noise is the VFD. I did not buy it though, because I thought I could try and fix it first.
---->> by
---->> by
You may also like:
In 3 leg three phase transformer, do we get some phase voltage magnitude and angle change due to un-symmetrical reluctance seen by every different phases? The phase at the middle leg is not distorted because ...
A frequency inverter controls AC motor speed. The frequency inverter converts the fixed supply frequency (60 Hz) to a variable-frequency, variable-voltage output to enable precise motor speed control. Many ...
Its beneficial to opt for the AC Drives as it supports SLVC [ VFD gives almost servo-like torque at low rpms if you give it encoder feedback ], multiple motors can be accessed, torque requirement can be met if ...
Negative sequence will not cause a physical rotation. This component creates a field which, though not strong enough, tries to counter the primary field, An increase in this component will cause the motor to ...
As a mathematical tool eventually, simulation can help to quickly approach the results that we need. If everything is done in right way, simulation can give us reliable conductive EMI results at the low ...
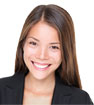
Featured
Like pumps, fans consume significant electrical energy while serving several applications. In many plants, the VFDs (variable ...
A frequency inverter controls AC motor speed. The frequency inverter converts the fixed supply frequency (60 Hz) to a ...
Motor starter (also known as soft starter, motor soft starter) is a electronic device integrates soft start, soft stop, ...
Soft starter allows the output voltage decreases gradually to achieve soft stop, in order to protect the equipment. Such as the ...
Soft Starter reduces electric motor starting current to 2-4 times during motor start up, reduces the impact to power grid during ...

In Discussion
Continuous process plant controls the plant without manual operations
Need help in Buck Vs. Flyback
Low cost controller with integrated switch
Medium Voltage Power Station
Differential Protection of 6600V Induction motor
Inductors with high volts-per-turn
Realtime intelligent alarming and guidance system for production process control
Solar panels for office with 7800 KW power consumption
Need help in Buck Vs. Flyback
Low cost controller with integrated switch
Medium Voltage Power Station
Differential Protection of 6600V Induction motor
Inductors with high volts-per-turn
Realtime intelligent alarming and guidance system for production process control
Solar panels for office with 7800 KW power consumption