System configuration of grounding
There are different types of system configuration for grounding like TT,IT,TN-C etc. How do we decide which configuration is suitable for the particular inverter (string or central). What are the factors that help us to decide the configurations?
One of the main concerns in a system is to avoid large low impedance ground loops.
These are created by the return signal path connected to the chassis (metal work) at multiple points. The large current loop allows noise currents to radiate H fields and hence couple into other electronics. The antenna effect will be proportional to loop area.
Single point grounding of the return path to chassis prevents this. However single point grounding conflicts with good RF practice where you want to ground to chassis at the sending and receiving ends of a signal path. There is therefore no universal best practice.
In my field, spacecraft, the standard practice has all primary power electronics galvanically isolated from the spacecraft chassis. Individual modules must maintain the isolation with transformer coupled DC/DC converters. The centre tap of each PSU secondary output is then single point grounded to the module metalwork. We talk about primary side and secondary side electronics where only secondary side is grounded to the metalwork.
Anything powered directly from the primary bus must be isolated with a maximum capacitance to chassis of 50nF to avoid excess HF loop currents forming.
In general it depends on country specific law and standards required by Power Supply Operators. From design point of view it all depends on which point of grid you are going to connect and what type of inverter is used.
One of the main concerns in a system is to avoid large low impedance ground loops.
These are created by the return signal path connected to the chassis (metal work) at multiple points. The large current loop allows noise currents to radiate H fields and hence couple into other electronics. The antenna effect will be proportional to loop area.
Single point grounding of the return path to chassis prevents this. However single point grounding conflicts with good RF practice where you want to ground to chassis at the sending and receiving ends of a signal path. There is therefore no universal best practice.
In my field, spacecraft, the standard practice has all primary power electronics galvanically isolated from the spacecraft chassis. Individual modules must maintain the isolation with transformer coupled DC/DC converters. The centre tap of each PSU secondary output is then single point grounded to the module metalwork. We talk about primary side and secondary side electronics where only secondary side is grounded to the metalwork.
Anything powered directly from the primary bus must be isolated with a maximum capacitance to chassis of 50nF to avoid excess HF loop currents forming.
In general it depends on country specific law and standards required by Power Supply Operators. From design point of view it all depends on which point of grid you are going to connect and what type of inverter is used.
You may also like:
Babbitt Bearings, properly cared for and maintained will last much longer than anti-friction bearings. Properly set up and aligned there is no contact between the babbitt and the journal other that a scuff ...
The Fuse for Electrical Motor is efficient for O/C (Short Circuit, either L-G or L-L) or/and internal fault in the Motor windings. Taking into consideration the fuse rating considering the Starting current of ...
Like pumps, fans consume significant electrical energy while serving several applications. In many plants, the VFDs (variable frequency drives) of fans together account for 50% to 60% of the total electricity ...
The UPS systems commissioning test and inspection procedures are to conform to;
• BS EN 50091-1:1993 - Specification for Uninterruptible Power Supplies (UPS). General and Safety Requirements, AND
• IEC ...
When two transformers are in a parallel group, a transformer with a higher tap position will typically have a higher (LV side) no-load voltage than the other one with a lower tap position. These unequal ...
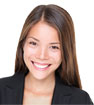
Featured
Like pumps, fans consume significant electrical energy while serving several applications. In many plants, the VFDs (variable ...
A frequency inverter controls AC motor speed. The frequency inverter converts the fixed supply frequency (60 Hz) to a ...
Motor starter (also known as soft starter, motor soft starter) is a electronic device integrates soft start, soft stop, ...
Soft starter allows the output voltage decreases gradually to achieve soft stop, in order to protect the equipment. Such as the ...
Soft Starter reduces electric motor starting current to 2-4 times during motor start up, reduces the impact to power grid during ...

In Discussion
Estimate ROI for BIPV (building integrated photovoltaic)?
HART Communication with Siemens PLC
Distributed Generation (DG)
Gas insulated HV Switch Gear
how can i calculate solar system size (Design)?
Buscoupler/Tie closing logic in auto transfer scheme
Minimum RPM through a VFD
Buchholz Relay Alarm in Winter
HART Communication with Siemens PLC
Distributed Generation (DG)
Gas insulated HV Switch Gear
how can i calculate solar system size (Design)?
Buscoupler/Tie closing logic in auto transfer scheme
Minimum RPM through a VFD
Buchholz Relay Alarm in Winter