Home » Blog » Energy saving » Sensorless motor control with TI and Microchip
Sensorless motor control with TI and Microchip
Question:
I need to learn about the sensorless control of permanent magnet AC (PMAC) motors. Can you recommend a tutorial and/or open source code for the sensorless motor control using the
a) TI TMS320 series processor, or
b) Microchip dsPIC33EP128 series processor?
Answer:
I have used Microchip and TMS320 to develop VFD for various applications. To give you a top level view, The TMS320 is a high end solution - a lot of commercial variable frequency drive uses TMS320 DSP. Quite a bit of work in programming, but if you go to the Ti web site and look at their new InstaspinFOC and InstaspinMotion, Ti have the entire motor control solution software implemented in ROM, you buy the chip, write a C program to call up their motor control function and you and a VFD. They provide you with a demo kit, PCB and a motor. It take me half a day to get the demo PCB running with my PMSM. Then I copy their design to my own.
The Microchip solution provides you with demo code. I used that before, but it require quite a bit of C programming, and motor tuning take even longer. The demo code and application note are no where near the performance of the Ti solution (I do not work for Ti -so I am not advertising). I take me a week to get my motor spinning with the demo kit from Microchip.
Then there are the International Rectifier solution that is available from many years. The IR sensorless motion control solution have implemented a FOC motor control in FPGA. So you don't need to write code for motor control. In the chip, it also has a 8051 cpu. You write the program in C; 1 page of code will get a washing machine working. It takes me 1 day to get a PMSM motor running with this solution.
I will use the TI solution for high end motor control - such as a US$40,000 dollar, 100HP direct drive PCP used in the oil field.
I will use the IR solution for a water pump, washing machine - things that is a few kw.
I will use the microchip for solution for toys, because Microchip is so much fun to play with.
I need to learn about the sensorless control of permanent magnet AC (PMAC) motors. Can you recommend a tutorial and/or open source code for the sensorless motor control using the
a) TI TMS320 series processor, or
b) Microchip dsPIC33EP128 series processor?
Answer:
I have used Microchip and TMS320 to develop VFD for various applications. To give you a top level view, The TMS320 is a high end solution - a lot of commercial variable frequency drive uses TMS320 DSP. Quite a bit of work in programming, but if you go to the Ti web site and look at their new InstaspinFOC and InstaspinMotion, Ti have the entire motor control solution software implemented in ROM, you buy the chip, write a C program to call up their motor control function and you and a VFD. They provide you with a demo kit, PCB and a motor. It take me half a day to get the demo PCB running with my PMSM. Then I copy their design to my own.
The Microchip solution provides you with demo code. I used that before, but it require quite a bit of C programming, and motor tuning take even longer. The demo code and application note are no where near the performance of the Ti solution (I do not work for Ti -so I am not advertising). I take me a week to get my motor spinning with the demo kit from Microchip.
Then there are the International Rectifier solution that is available from many years. The IR sensorless motion control solution have implemented a FOC motor control in FPGA. So you don't need to write code for motor control. In the chip, it also has a 8051 cpu. You write the program in C; 1 page of code will get a washing machine working. It takes me 1 day to get a PMSM motor running with this solution.
I will use the TI solution for high end motor control - such as a US$40,000 dollar, 100HP direct drive PCP used in the oil field.
I will use the IR solution for a water pump, washing machine - things that is a few kw.
I will use the microchip for solution for toys, because Microchip is so much fun to play with.
You may also like:
If you are interested in power electronics design at the board or system level, I would recommend LTspice (note the correct spelling) by far above all the others. In addition to being superb for IC design ...
Soft Starter reduces electric motor starting current to 2-4 times during motor start up, reduces the impact to power grid during motor start up, avoid the motor being burned out, and provide protection in ...
Due to variable frequency drive can adapt to various requirements in production process, especially in the industrial automation control applications, AC variable frequency control technology has risen to be ...
The key to optimizing the system operation is communication and information sharing through the entire system equipment. With the reduced cost of variable frequency drives and Building Automation Systems, ...
I am assuming that the trip circuit is floating DC (ungrounded). If so, the moisture could be causing a "sneak" circuit, otherwise known as a "hot short" in the tripping circuit, which essentially bypasses the ...
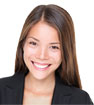
Featured
Like pumps, fans consume significant electrical energy while serving several applications. In many plants, the VFDs (variable ...
A frequency inverter controls AC motor speed. The frequency inverter converts the fixed supply frequency (60 Hz) to a ...
Motor starter (also known as soft starter, motor soft starter) is a electronic device integrates soft start, soft stop, ...
Soft starter allows the output voltage decreases gradually to achieve soft stop, in order to protect the equipment. Such as the ...
Soft Starter reduces electric motor starting current to 2-4 times during motor start up, reduces the impact to power grid during ...

In Discussion
General purpose software tool for designing multiple output flyback converters
What is the relationship between inducer and NPSH?
Simulation and Modelling, who uses it, and for what?
Voltage Frequency Calculations
VALUE ENGINEERING ON CABLING SYSTEM FOR POWER PLANT
Network based remote access to industrial automation systems
Insulation Resistance of generator stator drops
Advantages/Disadvantages of String inverters vs. Central inverters?
What is the relationship between inducer and NPSH?
Simulation and Modelling, who uses it, and for what?
Voltage Frequency Calculations
VALUE ENGINEERING ON CABLING SYSTEM FOR POWER PLANT
Network based remote access to industrial automation systems
Insulation Resistance of generator stator drops
Advantages/Disadvantages of String inverters vs. Central inverters?