Home » Blog » Motor controls » Ratio of stator coils and rotor poles in three phase axial flux PM motor design
Ratio of stator coils and rotor poles in three phase axial flux PM motor design
Question:
I am currently investigating the design of a three phase axial flux PM motor, but replacing conventional materials with high temperature superconductors. I'm interested to know the thoughts of group members regarding design rules/rules of thumb relating to the number of stator coils and rotor poles. Many in the amateur wind turbine community seem to use a 4:3 ratio (magnets:coils), but I can't seem to find anything 'official' on the topic.
An equal number of magnets: coils would cause problems with starting the motor and with cogging/torque pulsations.
The only textbook I've found dedicated to the design of axial flux PM motors is Jacek Gieras's book on 'Axial Flux Permanent Magnet Brushless Machines', but this seems only to mention examples of coils: poles ratios (e.g., 12 stator coils and 8 rotor poles, 9/8, etc.).
Answer:
"Design of Brushless Permanent-Magnet Motors" by J.R. Hendershot Jr. and TJE Miller is an excellent design book and pages 3-50 thru 3-55 illustrate the 3 phase winding patterns you describe (8/6, 8/9, and 4/6). Whether axial air gap or radial air gap the principles are the same. I assume with an axial air gap machine you do not want phases overlapping each other, that is the common factor in the three patterns above. This keeps winding simple and compact and is commonly used on smaller 3 phase brushless motors.
These windings do not automatically guarantee a true BEMF sine wave form. If you want a sinusoidal waveform you will have to do some work on tailoring the magnetic design (gap between magnets, skewing, air gap profiling, etc.). Some servo motor manufacturers do just this to get a true BEMF sine wave to match their sine wave controllers for ripple free torque operation.
Another decision is does the coil center have a laminated steel pole or only and air center. Air gap windings should be axially thin and have no hysteresis component which is good for high speed operation. A slotted pole winding can handle more wire bulk but a laminated construction may be difficult to implement, you might look at an AC Powdered Metal for the Armature and teeth.
If you allow phase coils to overlap there are a great many other winding patterns possible (listed in the reference book), some are better for Trapezoid controller drive and some are better for sine wave controller drive (BEMF should match controller drive type). Just depends on you end goals.
I am currently investigating the design of a three phase axial flux PM motor, but replacing conventional materials with high temperature superconductors. I'm interested to know the thoughts of group members regarding design rules/rules of thumb relating to the number of stator coils and rotor poles. Many in the amateur wind turbine community seem to use a 4:3 ratio (magnets:coils), but I can't seem to find anything 'official' on the topic.
An equal number of magnets: coils would cause problems with starting the motor and with cogging/torque pulsations.
The only textbook I've found dedicated to the design of axial flux PM motors is Jacek Gieras's book on 'Axial Flux Permanent Magnet Brushless Machines', but this seems only to mention examples of coils: poles ratios (e.g., 12 stator coils and 8 rotor poles, 9/8, etc.).
Answer:
"Design of Brushless Permanent-Magnet Motors" by J.R. Hendershot Jr. and TJE Miller is an excellent design book and pages 3-50 thru 3-55 illustrate the 3 phase winding patterns you describe (8/6, 8/9, and 4/6). Whether axial air gap or radial air gap the principles are the same. I assume with an axial air gap machine you do not want phases overlapping each other, that is the common factor in the three patterns above. This keeps winding simple and compact and is commonly used on smaller 3 phase brushless motors.
These windings do not automatically guarantee a true BEMF sine wave form. If you want a sinusoidal waveform you will have to do some work on tailoring the magnetic design (gap between magnets, skewing, air gap profiling, etc.). Some servo motor manufacturers do just this to get a true BEMF sine wave to match their sine wave controllers for ripple free torque operation.
Another decision is does the coil center have a laminated steel pole or only and air center. Air gap windings should be axially thin and have no hysteresis component which is good for high speed operation. A slotted pole winding can handle more wire bulk but a laminated construction may be difficult to implement, you might look at an AC Powdered Metal for the Armature and teeth.
If you allow phase coils to overlap there are a great many other winding patterns possible (listed in the reference book), some are better for Trapezoid controller drive and some are better for sine wave controller drive (BEMF should match controller drive type). Just depends on you end goals.
You may also like:
Many years ago I had an experience of 4nos 37kW fin-fan motors wrongly connected at site to a star. After running for almost 1 year, the operators reported these motors were very warm and felt unusual. We ...
When two transformers are in a parallel group, a transformer with a higher tap position will typically have a higher (LV side) no-load voltage than the other one with a lower tap position. These unequal ...
The biggest differences between the floor programmer and the office programmer is often a piece of paper (knowledge and experience do not replace a piece of paper in the mind of HR person that has no ...
The UPS systems commissioning test and inspection procedures are to conform to;
• BS EN 50091-1:1993 - Specification for Uninterruptible Power Supplies (UPS). General and Safety Requirements, AND
• IEC ...
Like pumps, fans consume significant electrical energy while serving several applications. In many plants, the VFDs (variable frequency drives) of fans together account for 50% to 60% of the total electricity ...
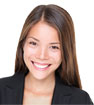
Featured
Like pumps, fans consume significant electrical energy while serving several applications. In many plants, the VFDs (variable ...
A frequency inverter controls AC motor speed. The frequency inverter converts the fixed supply frequency (60 Hz) to a ...
Motor starter (also known as soft starter, motor soft starter) is a electronic device integrates soft start, soft stop, ...
Soft starter allows the output voltage decreases gradually to achieve soft stop, in order to protect the equipment. Such as the ...
Soft Starter reduces electric motor starting current to 2-4 times during motor start up, reduces the impact to power grid during ...

In Discussion
Why are harmonics produced in a transformer?
How do you handle loop interactions?
Difference between safety grounding switch & high speed grounding switch in HV GIS
How we calculate orifice plate dia, bore and flow of steam?
Viscosity Effect on Centrifugal Pump Performance?
How to approach Pump manufacturers on electrical control systems?
Often-overlooked Risks in an Automation Project, and how to find them
Mentoring, a valuable source of learning and maturing as an engineer.
How do you handle loop interactions?
Difference between safety grounding switch & high speed grounding switch in HV GIS
How we calculate orifice plate dia, bore and flow of steam?
Viscosity Effect on Centrifugal Pump Performance?
How to approach Pump manufacturers on electrical control systems?
Often-overlooked Risks in an Automation Project, and how to find them
Mentoring, a valuable source of learning and maturing as an engineer.