Home » Blog » Experience » Power supply prototypes is the best way to learn it
Power supply prototypes is the best way to learn it
I have been designing power supplies for over 15 years now. We do mostly off line custom designs ranging from 50 to 500W. Often used in demanding environments such as offshore and shipping.
I think we are the lucky ones who got the chance to learn designing power supplies using the simple topologies like a flyback or a forward converter. If we wanted to make something fancy we used a push-pull or a half bridge.
Nowadays, straight out of school you get to work on a resonant converter, working with variable frequency control. Frequencies are driven up above 250kHz to make it fit in a matchbox, still delivering 100W or more. PCB layouts get almost impossible to make if you also have to think about costs and manufacturability.
Now the digital controllers are coming into fashion. These software designers know very little about power electronics and think they can solve every problem with a few lines of code.
But I still think the best way to learn is to start at the basics and do some through testing on the prototypes you make. In my department we have a standard test program to check if the prototype functions according to the specifications (Design Verification Tests), but also if all parts are used within their specifications (Engineering Verification Tests). These tests are done at the limits of input voltage range and output power. And be aware that the limit of the output power is not just maximum load, but also overload, short circuit and zero load! Start-up and stability are tested at low temperature and high temperature.
With today's controllers the datasheets seem to get ever more limited in information, and the support you get from the FAE's is often very disappointing. Sometime ago I even had one in the lab who sat next to me for half a day to solve a mysterious blow up of a high side driver. At the end of the day he thanked me, saying he had learned a lot!
Not the result I was hoping for.
I think we are the lucky ones who got the chance to learn designing power supplies using the simple topologies like a flyback or a forward converter. If we wanted to make something fancy we used a push-pull or a half bridge.
Nowadays, straight out of school you get to work on a resonant converter, working with variable frequency control. Frequencies are driven up above 250kHz to make it fit in a matchbox, still delivering 100W or more. PCB layouts get almost impossible to make if you also have to think about costs and manufacturability.
Now the digital controllers are coming into fashion. These software designers know very little about power electronics and think they can solve every problem with a few lines of code.
But I still think the best way to learn is to start at the basics and do some through testing on the prototypes you make. In my department we have a standard test program to check if the prototype functions according to the specifications (Design Verification Tests), but also if all parts are used within their specifications (Engineering Verification Tests). These tests are done at the limits of input voltage range and output power. And be aware that the limit of the output power is not just maximum load, but also overload, short circuit and zero load! Start-up and stability are tested at low temperature and high temperature.
With today's controllers the datasheets seem to get ever more limited in information, and the support you get from the FAE's is often very disappointing. Sometime ago I even had one in the lab who sat next to me for half a day to solve a mysterious blow up of a high side driver. At the end of the day he thanked me, saying he had learned a lot!
Not the result I was hoping for.
You may also like:
For the AC power line, the system (VFD + motor) is a non-linear load whose current include harmonics (frequency components multiples of the power line frequency). The characteristic harmonics generally ...
The guy asked for suggestions on how to improve troubleshooting techniques. I mentioned this earlier as a "suggestion" for starters but the idea got lost in all the complaining and totally irrelevant responses ...
Many years ago we used to call this the "what ifs?". Part of the design phase is when we model what we think the system is meant to do. Just as important is how the system is meant to react when things are not ...
Synchronous motors generally offer more efficiency than induction ones, and hence in higher ratings (about 5000 hp and higher) they may be more cost effective considering Life Cycle Costs. The exact size of ...
DC drives with motor field control provide coordinated automatic armature & field voltage control for extended speed range & constant-horsepower applications. The motor is armature-voltage-controlled ...
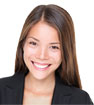
Featured
Like pumps, fans consume significant electrical energy while serving several applications. In many plants, the VFDs (variable ...
A frequency inverter controls AC motor speed. The frequency inverter converts the fixed supply frequency (60 Hz) to a ...
Motor starter (also known as soft starter, motor soft starter) is a electronic device integrates soft start, soft stop, ...
Soft starter allows the output voltage decreases gradually to achieve soft stop, in order to protect the equipment. Such as the ...
Soft Starter reduces electric motor starting current to 2-4 times during motor start up, reduces the impact to power grid during ...

In Discussion
How to optimize the power dissipated in a switching MOSFET transistor?
Solar PV installers
Should Automation Consultants align themselves to system vendors for marketing and discount gains?
Convert single phase motor wound aluminum wire to copper magnet wire
Reliance Auotmax PLC (with MB+ protocol) to communicate via TCP/IP?
Anyone making DC submersible pump motors?
Off-grid system concept
What is a Silent Pole Generator?
Solar PV installers
Should Automation Consultants align themselves to system vendors for marketing and discount gains?
Convert single phase motor wound aluminum wire to copper magnet wire
Reliance Auotmax PLC (with MB+ protocol) to communicate via TCP/IP?
Anyone making DC submersible pump motors?
Off-grid system concept
What is a Silent Pole Generator?