Power supply prototype failures
I remember my very first power supply. They threw me in the deep end in 1981 building a multi-output 1 kW power supply. I was fresh from college, thought i knew everything, and consumed publications voraciously to learn more. Exciting times.
But nothing prepared me for the hardware trials and tribulations. We built things and they blew up. Literally. We would consume FETs and controllers at an alarming rate. The rep from Unitrode would come and visit and roll his eyes when we told him we needed another dozen controllers since yesterday.
The reasons for failure were all over the map . EMI, heat, layout issues, design issues, bad components (we had some notorious early GE parts - they exited the market shortly afterwards.)
Some of the issues took a few days to fix, some of them took weeks. We had two years to get the product ready, which was faster than the computer guys were doing their part, so it was OK.
90% of the failure issues weren't talked about in any paper, and to this day, most of them still aren't.
So, fast forward to today, 32 years later. I still like to build hardware - you can't teach what you don't practise regularly, so I keep at it.
With all the benefit of 3 decades of knowledge I STILL blow things up. Everything progresses along fine, then i touch a sensitive circuit node, or miss some critical design point and off it goes. I'm faster now at finding the mistakes but I still find there are new ones to be made. And when it blows up with 400 V applied, it's a mess and a few hours to rebuild. Or you have to start over sometimes, if the PCB traces are vaporized.
So my first prototype, while on a PC board, always includes the controller in a socket because I know I will need that. Magnetics too, when possible, I know I'll revise them time and again to tweak performance. PC boards will be a minimum of two passes, probably three.
But nothing prepared me for the hardware trials and tribulations. We built things and they blew up. Literally. We would consume FETs and controllers at an alarming rate. The rep from Unitrode would come and visit and roll his eyes when we told him we needed another dozen controllers since yesterday.
The reasons for failure were all over the map . EMI, heat, layout issues, design issues, bad components (we had some notorious early GE parts - they exited the market shortly afterwards.)
Some of the issues took a few days to fix, some of them took weeks. We had two years to get the product ready, which was faster than the computer guys were doing their part, so it was OK.
90% of the failure issues weren't talked about in any paper, and to this day, most of them still aren't.
So, fast forward to today, 32 years later. I still like to build hardware - you can't teach what you don't practise regularly, so I keep at it.
With all the benefit of 3 decades of knowledge I STILL blow things up. Everything progresses along fine, then i touch a sensitive circuit node, or miss some critical design point and off it goes. I'm faster now at finding the mistakes but I still find there are new ones to be made. And when it blows up with 400 V applied, it's a mess and a few hours to rebuild. Or you have to start over sometimes, if the PCB traces are vaporized.
So my first prototype, while on a PC board, always includes the controller in a socket because I know I will need that. Magnetics too, when possible, I know I'll revise them time and again to tweak performance. PC boards will be a minimum of two passes, probably three.
You may also like:
Well, depending on the power rating, and on the required reliability, I believe it's very simply. The biggest problem would be to get a variable frequency drive, or other power supply to provide a 3-phase ...
1. Voltage unbalance in supply side (1% volts could easily be 10% current).
2. Physical differences between individual stator coil shapes and connections causing small (but noticeable) resistance changes. ...
Variable speed drive switches very fast which brings high dv/dt on motor. How often do we face with problems coming with VSD? How harmful is the common mode currents in windings and other parts of motor due to ...
The high frequency edges of switched waveforms can cause capacitively coupled currents to flow from windings to frame, returning through the bearings, and these can accelerate corrosion in the bearings, ...
For a "physical" interpretation, reactive current (power/KVA flow), in my opinion is best looked at from the perspective of a generator connected directly to an infinite bus (in LV generators this is the norm).
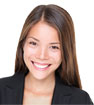
Featured
Like pumps, fans consume significant electrical energy while serving several applications. In many plants, the VFDs (variable ...
A frequency inverter controls AC motor speed. The frequency inverter converts the fixed supply frequency (60 Hz) to a ...
Motor starter (also known as soft starter, motor soft starter) is a electronic device integrates soft start, soft stop, ...
Soft starter allows the output voltage decreases gradually to achieve soft stop, in order to protect the equipment. Such as the ...
Soft Starter reduces electric motor starting current to 2-4 times during motor start up, reduces the impact to power grid during ...

In Discussion
Design Implications in Sub Micron Positioning
What's the alternative for a solar system?
Looking for 4 Mw PV modules 250Wp poly EU production
400 kV transmission line charging
Alternative Energy field (Solar, Wind and Hydro)
In case Copper, annealed soft-drawn...
What are 3 of the biggest risks when investing in PV energy?
Controlling exotherm in a batch reactor using cooling water
What's the alternative for a solar system?
Looking for 4 Mw PV modules 250Wp poly EU production
400 kV transmission line charging
Alternative Energy field (Solar, Wind and Hydro)
In case Copper, annealed soft-drawn...
What are 3 of the biggest risks when investing in PV energy?
Controlling exotherm in a batch reactor using cooling water