Home » Blog » Energy saving » Power converter trend
Power converter trend
The trend toward lower losses in power converters is not apparent in all of the applications of power converters. It is also not apparent that the power converter solution and its losses for a given market will be the same when it comes to losses. In terms of the market shift that you mention, Prof. the answer is probably that each market is becoming split into a lower efficiency and higher efficiency solution.
From my limited view the reason for this is the effort and time required to do the low loss development. The early developers of low loss converters are now ahead and those that were slower may never catch them. This gap is in a number of converter markets widening, with both higher loss and lower loss offerings continuing to be used and sold. This split is not apparent with different levels of development or geographically.
Some markets already have very efficient solutions, other markets not so efficient and others had high power loss solutions. The customers accepted these solutions. The path to lower loss converters is for some markets not yet clear and in some markets the requirement may never actually become real.
It does seem that there is a real case to make for any power converter market splitting in two as the opportunities presented by lowering the power loss are taken.
All low loss converters present significant challenges and are all somewhat esoteric.
For me power supply EMI control consists of designing filtering for differential and common mode conducted emissions. The differential mode filtering attenuates the primary side differential lower frequency switching current fundamental & harmonic frequencies. The common mode filtering provides a low impedance return path for high frequency noise currents resulting from high dV/dt transitions during switching transitions present on the power semiconductors (switching mosfet drain, rectifier cathods). These noise currents ring at high frequencies as they oscillate in the uncontrolled parasitic inductance and capacitance associated with their return to source path. Shortening and damping this return path allows the high frequency noise currents to return locally instead of via the measurement copper bench and conducted emi current or voltage (LISN) probe as well as providing a more damped ringing frequency. Shorting this return path has the added benefit of decreasing radiated emissions. In addition proper layout of the power train so as to minimize the loop area associated with both the primary and secondary side switching currents minimizes the associated radiated emissions.
When I mentioned the criticism of resonant mode converter as related to the challenges of emi filitering I was referring to the additional differential mode filtering required. For example if you take a square wave primary side current waveform and analyze the differential frequency content the fundamental magnitude with be lower and there will be higher frequency components as compared to a purely resonant approach at the same power level. It is normally the lower frequency content that has to be filtered differentially.
Given these differences the additional emi filtering volume/cost of the resonant approach may pose a disadvantage.
From my limited view the reason for this is the effort and time required to do the low loss development. The early developers of low loss converters are now ahead and those that were slower may never catch them. This gap is in a number of converter markets widening, with both higher loss and lower loss offerings continuing to be used and sold. This split is not apparent with different levels of development or geographically.
Some markets already have very efficient solutions, other markets not so efficient and others had high power loss solutions. The customers accepted these solutions. The path to lower loss converters is for some markets not yet clear and in some markets the requirement may never actually become real.
It does seem that there is a real case to make for any power converter market splitting in two as the opportunities presented by lowering the power loss are taken.
All low loss converters present significant challenges and are all somewhat esoteric.
For me power supply EMI control consists of designing filtering for differential and common mode conducted emissions. The differential mode filtering attenuates the primary side differential lower frequency switching current fundamental & harmonic frequencies. The common mode filtering provides a low impedance return path for high frequency noise currents resulting from high dV/dt transitions during switching transitions present on the power semiconductors (switching mosfet drain, rectifier cathods). These noise currents ring at high frequencies as they oscillate in the uncontrolled parasitic inductance and capacitance associated with their return to source path. Shortening and damping this return path allows the high frequency noise currents to return locally instead of via the measurement copper bench and conducted emi current or voltage (LISN) probe as well as providing a more damped ringing frequency. Shorting this return path has the added benefit of decreasing radiated emissions. In addition proper layout of the power train so as to minimize the loop area associated with both the primary and secondary side switching currents minimizes the associated radiated emissions.
When I mentioned the criticism of resonant mode converter as related to the challenges of emi filitering I was referring to the additional differential mode filtering required. For example if you take a square wave primary side current waveform and analyze the differential frequency content the fundamental magnitude with be lower and there will be higher frequency components as compared to a purely resonant approach at the same power level. It is normally the lower frequency content that has to be filtered differentially.
Given these differences the additional emi filtering volume/cost of the resonant approach may pose a disadvantage.
You may also like:
My cable size and transformer size should give me maximum 3% on the worst 6% to 10%. If it is the single only equipment on the system then maybe you can tolerate 15%. If not, dip factor may affect sensitive ...
A low impedance fault is usually a bolted fault, which is a short circuit. It allows a high amount of fault current to flow, and an upstream breaker or fuse usually senses the high current and operates, ending ...
Resistance Grounding Systems have many advantages over solidly grounded systems including arc-flash hazard reduction, limiting mechanical and thermal damage associated with faults, and controlling transient ...
If you're planning to use a Soft Starter or VFD for motor starting, you need to specify the horsepower rating, voltage rating, rated frequency, the type of motor (induction wound rotor or induction squirrel ...
Soft Start and Soft Stop is especially useful with pumping fluids where torque transients often cause water hammer effects, and in some instances, failure to gradually slow the fluid down before stopping, can ...
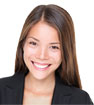
Featured
Like pumps, fans consume significant electrical energy while serving several applications. In many plants, the VFDs (variable ...
A frequency inverter controls AC motor speed. The frequency inverter converts the fixed supply frequency (60 Hz) to a ...
Motor starter (also known as soft starter, motor soft starter) is a electronic device integrates soft start, soft stop, ...
Soft starter allows the output voltage decreases gradually to achieve soft stop, in order to protect the equipment. Such as the ...
Soft Starter reduces electric motor starting current to 2-4 times during motor start up, reduces the impact to power grid during ...

In Discussion
How Can be selected the system battery voltage for Module
Looking for Dc Motor manufacturer that can supply motor for hydraulic pump
Design high current air cored inductor
Settings of Battery Bank AH capacity made on the Solar Charge Controller
Determine power factor of generator(s)?
Transformer
What are the specifications for instrument cables in oil & gas plants?
D2PAK and DPAK high power diodes
Looking for Dc Motor manufacturer that can supply motor for hydraulic pump
Design high current air cored inductor
Settings of Battery Bank AH capacity made on the Solar Charge Controller
Determine power factor of generator(s)?
Transformer
What are the specifications for instrument cables in oil & gas plants?
D2PAK and DPAK high power diodes