Operate low speed generator and high speed generator in the same terminal
Can we operate low speed generator and high speed generator in the same terminal? Is there a mechanical effect?
First, specify that this is an isolated system with two generators feeding the same bus. Operation of an isolated system is different than a grid connected system, and the mode setting of the governors have to be set to accommodate this. Depending upon the prime mover type and governor model, improper tuning will manifest itself in speed variations. The size of the two machines relative to each other, as well as their size relative to the load, can have measurable impact as well. The best way to tell whether it is mechanical or electrical in nature is to look at the time-frame of the phenomena relative to the time constants of the various control and response loops.
Second, "...In large power system, generators are not connected in the same terminal..." is not generally true, there are many power plants where multiple generators feed the same bus before the power is utilized.
Third, "...frequency oscillation is about 1.5-2 Hz...", if you mean that the frequency swings between 48 and 52 Hz routinely, that usually indicates a governor setup/tuning problem or a non-uniform load.
Fourth, reactive current compensation takes place in quadrature from real power and should have minimal effect on real power and only affect the terminal voltage if not set properly. Droop compensation is the means for ensuring that the AVRs do not fight with each other since you cannot have two independent controllers attempting to control the same control variable.
Fifth, regarding different types of prime movers, some are inherently more likely to induce mechanical vibrations, especially reciprocating engines, especially if they are not all of the same size and/or number of cylinders. The same is true of the loads, non-uniform, cyclic loads can cause very severe problems especially on isolated systems where the load is a significant percentage of the prime movers' output power. The analysis of, and solution to, such problems is an interesting area of study.
First, specify that this is an isolated system with two generators feeding the same bus. Operation of an isolated system is different than a grid connected system, and the mode setting of the governors have to be set to accommodate this. Depending upon the prime mover type and governor model, improper tuning will manifest itself in speed variations. The size of the two machines relative to each other, as well as their size relative to the load, can have measurable impact as well. The best way to tell whether it is mechanical or electrical in nature is to look at the time-frame of the phenomena relative to the time constants of the various control and response loops.
Second, "...In large power system, generators are not connected in the same terminal..." is not generally true, there are many power plants where multiple generators feed the same bus before the power is utilized.
Third, "...frequency oscillation is about 1.5-2 Hz...", if you mean that the frequency swings between 48 and 52 Hz routinely, that usually indicates a governor setup/tuning problem or a non-uniform load.
Fourth, reactive current compensation takes place in quadrature from real power and should have minimal effect on real power and only affect the terminal voltage if not set properly. Droop compensation is the means for ensuring that the AVRs do not fight with each other since you cannot have two independent controllers attempting to control the same control variable.
Fifth, regarding different types of prime movers, some are inherently more likely to induce mechanical vibrations, especially reciprocating engines, especially if they are not all of the same size and/or number of cylinders. The same is true of the loads, non-uniform, cyclic loads can cause very severe problems especially on isolated systems where the load is a significant percentage of the prime movers' output power. The analysis of, and solution to, such problems is an interesting area of study.
You may also like:
Overload protection: the soft starter has current control loop to track and detect of the changes of the electric motor current. Achieve overload protection by increasing overload current settings and inverse ...
It depends on so much more than the simple requirements listed of high starting torque and variable speed. What kind of application are you using it for? Is it on an automobile (where you have DC already), a ...
Stiff voltage sources are not problematic as long as they don't get in the way of the solver's attempts to linearize the behavior of the circuit matrix via step size reduction. It is the highly nonlinear stiff ...
Variable frequency drives are electronic devices, they have stringent requirements in installation environment which is specified in its user manual normally. In exceptional circumstances, if it does not meet ...
Generally, electric motors are designed according to 50Hz power supply, its rated torque also in this frequency. Therefore, the speed adjustment under rated frequency called constant torque speed adjustment. ...
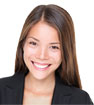
Featured
Like pumps, fans consume significant electrical energy while serving several applications. In many plants, the VFDs (variable ...
A frequency inverter controls AC motor speed. The frequency inverter converts the fixed supply frequency (60 Hz) to a ...
Motor starter (also known as soft starter, motor soft starter) is a electronic device integrates soft start, soft stop, ...
Soft starter allows the output voltage decreases gradually to achieve soft stop, in order to protect the equipment. Such as the ...
Soft Starter reduces electric motor starting current to 2-4 times during motor start up, reduces the impact to power grid during ...

In Discussion
Difference between Numerical calculating and FEA almost %10 error, Why?
unbalanced load distribution among three phases in a building
PMSM initial rotor alignment: what is the correct strategy?
DCS
DTC vs. classic PWM vector VFD
Connection between Reactive Power and Vibration
Pros and Cons of Self-priming Centrifugal Pumps
use of varistors in SPICE simulations
unbalanced load distribution among three phases in a building
PMSM initial rotor alignment: what is the correct strategy?
DCS
DTC vs. classic PWM vector VFD
Connection between Reactive Power and Vibration
Pros and Cons of Self-priming Centrifugal Pumps
use of varistors in SPICE simulations