Home » Blog » Motor controls » Motor design
Motor design
When I was doing my PhD in motor design of reluctance machines with flux assistance (switched reluctance machines and flux switching machines with magnets and/or permanently energised coils) my supervisor was doing research on the field of sensorless control (it wasn't the area of my research but it got me thinking about it all). At the time I had thought (only in my head as a PhD student daydream) that I would have to initially force a phase (or phases) to deliberately set the rotor into a known position due to the phase firing then start a normal phase firing sequences to start and operate the motor for a normal load without the need for any form position detection (all this was assuming I had the motor running from stationary to full speed at normal expected load with use of a position sensor to start with so I could link phase firing, rotor position and timings all together to create a "map" which I could then try to use to re-program a firing sequence with no position detection at all but only if I could force the rotor to "park" itself in the same position every time before starting the machine properly - the "map" having the information to assume that the motor changes speed correctly as it changes the firing sequences as it accelerates to full speed). But any problem such as unusual load condition or fault condition (e.g. short circuit or open circuit in a phase winding) would render useless such an attempt at control with no form of position detection at all. The induction machine being sensorless and on the grid being measured.
You may also like:
Ahh I see the words machine tool and shop floor; now I can see where you guys are coming from. The type of machines that you talk about were controlled by relay logic and then when technology arrived the ...
Make sure your generator can start your largest motor and that your disconnect breaker or fuses can handle the inrush. I have seen this as an issue, especially when soft starters are used. Soft starters lower ...
DC drives vary the speed of DC motors with greater efficiency & speed regulation than resistor control circuits. Since the speed of a DC motor is directly proportional to armature voltage & inversely ...
I never just put power to a first prototype and see what happens. Smoke and loud sounds are the most likely result and then you just know that something was not perfect. So how would you test the next ...
Controlled bridge rectifiers are not limited to single-phase designs. In most commercial & industrial control systems, AC power is available in three-phase form for maxi mum horsepower & efficiency. ...
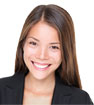
Featured
Like pumps, fans consume significant electrical energy while serving several applications. In many plants, the VFDs (variable ...
A frequency inverter controls AC motor speed. The frequency inverter converts the fixed supply frequency (60 Hz) to a ...
Motor starter (also known as soft starter, motor soft starter) is a electronic device integrates soft start, soft stop, ...
Soft starter allows the output voltage decreases gradually to achieve soft stop, in order to protect the equipment. Such as the ...
Soft Starter reduces electric motor starting current to 2-4 times during motor start up, reduces the impact to power grid during ...

In Discussion
Microlense coated PV panels compared to traditional flat surface panels
ICAPS simulator question
High efficiency DC-DC converter - Topology recommendation
Over voltage and under voltage protection for line fed equipments
Is the Automation industry growing?
Manufacturing process for BLDC Motors
Keep the Documentation Clear and Simple
AODD To Electric Driven Pump
ICAPS simulator question
High efficiency DC-DC converter - Topology recommendation
Over voltage and under voltage protection for line fed equipments
Is the Automation industry growing?
Manufacturing process for BLDC Motors
Keep the Documentation Clear and Simple
AODD To Electric Driven Pump