Home » Blog » Experience » How to get confidence while powering ON an SMPS prototype?
How to get confidence while powering ON an SMPS prototype?
I never just put power to a first prototype and see what happens. Smoke and loud sounds are the most likely result and then you just know that something was not perfect. So how would you test the next prototype sample?
A good idea is to put supply voltage to your control circuit from an external supply first - often something like 12V. Check oscillator waveform, frequency, gate pulses etc. If possible, use another external power supply to put a voltage to your output. Increasing this voltage slowly, you should see the gate pulses go from max. to min. duty cycle when passing the desired output voltage. If this does not happen, check your feedback path, still without turning main power on.
If everything looks as expected, remove the external supply from the output but keep the control circuit powered from an external source. Then SLOWLY turn up the main input voltage while using your oscilloscope to monitor the voltage waveforms in the power circuit and a DC voltmeter to monitor output voltage etc. Keep an eye on the ampere-meter on the main power source. If something suspicious occurs, stop increasing input further and investigate what's happening while the circuit is still alive.
With a low load you should normally expect the output voltage to hit the desired value soon, at least in a flyback converter. Check that this happens. Then check what happens with a variable load - preferably electronic.
If you did not calculate your feedback loop, very likely you will see self oscillation (normally not destructive). If you don't, use the step load function in your electronic load to check stability. If you see a clear ringing after a load step, you still have some work to do in your loop. But feedback and stability is another huge area which Mr. Ridley has taught us a lot about.
And yes - the world needs powerful POWER ENGINEERS desperately!
A good idea is to put supply voltage to your control circuit from an external supply first - often something like 12V. Check oscillator waveform, frequency, gate pulses etc. If possible, use another external power supply to put a voltage to your output. Increasing this voltage slowly, you should see the gate pulses go from max. to min. duty cycle when passing the desired output voltage. If this does not happen, check your feedback path, still without turning main power on.
If everything looks as expected, remove the external supply from the output but keep the control circuit powered from an external source. Then SLOWLY turn up the main input voltage while using your oscilloscope to monitor the voltage waveforms in the power circuit and a DC voltmeter to monitor output voltage etc. Keep an eye on the ampere-meter on the main power source. If something suspicious occurs, stop increasing input further and investigate what's happening while the circuit is still alive.
With a low load you should normally expect the output voltage to hit the desired value soon, at least in a flyback converter. Check that this happens. Then check what happens with a variable load - preferably electronic.
If you did not calculate your feedback loop, very likely you will see self oscillation (normally not destructive). If you don't, use the step load function in your electronic load to check stability. If you see a clear ringing after a load step, you still have some work to do in your loop. But feedback and stability is another huge area which Mr. Ridley has taught us a lot about.
And yes - the world needs powerful POWER ENGINEERS desperately!
You may also like:
DC drives vary the speed of DC motors with greater efficiency & speed regulation than resistor control circuits. Since the speed of a DC motor is directly proportional to armature voltage & inversely ...
Ahh I see the words machine tool and shop floor; now I can see where you guys are coming from. The type of machines that you talk about were controlled by relay logic and then when technology arrived the ...
When I was doing my PhD in motor design of reluctance machines with flux assistance (switched reluctance machines and flux switching machines with magnets and/or permanently energised coils) my supervisor was ...
The trend toward lower losses in power converters is not apparent in all of the applications of power converters. It is also not apparent that the power converter solution and its losses for a given market ...
My cable size and transformer size should give me maximum 3% on the worst 6% to 10%. If it is the single only equipment on the system then maybe you can tolerate 15%. If not, dip factor may affect sensitive ...
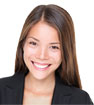
Featured
Like pumps, fans consume significant electrical energy while serving several applications. In many plants, the VFDs (variable ...
A frequency inverter controls AC motor speed. The frequency inverter converts the fixed supply frequency (60 Hz) to a ...
Motor starter (also known as soft starter, motor soft starter) is a electronic device integrates soft start, soft stop, ...
Soft starter allows the output voltage decreases gradually to achieve soft stop, in order to protect the equipment. Such as the ...
Soft Starter reduces electric motor starting current to 2-4 times during motor start up, reduces the impact to power grid during ...

In Discussion
Which types of pumps are used in chilled water systems?
AODD To Electric Driven Pump
transformer back charging
How much will the solar panel will cost and its production capacity
RoHS directive for power supplies
ICAPS simulator question
D2PAK and DPAK high power diodes
Microlense coated PV panels compared to traditional flat surface panels
AODD To Electric Driven Pump
transformer back charging
How much will the solar panel will cost and its production capacity
RoHS directive for power supplies
ICAPS simulator question
D2PAK and DPAK high power diodes
Microlense coated PV panels compared to traditional flat surface panels