High starting torque, synchronous motor, induction motor or DC motor?
It depends on so much more than the simple requirements listed of high starting torque and variable speed. What kind of application are you using it for? Is it on an automobile (where you have DC already), a factory, and do you have the budget and/or space for a variable frequency drive. A synchronous servo motor gives great dynamic control and great starting torque per volume, but its speed range is limited (unless you're field weakening by the back EMF). Servo-motors are also the most expensive due to their position sensors and more intelligent drives.
With a proper soft drive you can go with an induction motor, but it depends. if power is small you can go to step motor also. But dc series motor's starting torque is high as expressed others.
DC Series motors have high starting torque but induction motors have wide range of speed control. So, If DC motor is used, then DC drives you can use, although it will be expensive and DC motors are tough to maintain than ac motors due to commutation Problem.
DC series motor would provide both the high starting torque and adjustable speed BUT beware that DC motors have high maintenance cost and also require AC-DC conversion. You could use other available options e.g. double wound induction motors etc, depending upon your requirements.
But today, there is no application where you cannot apply AC motors, asynchronous or synchronous. If the motor and the associated power electronics are correctly rated, you can have any starting torque you want.
The typical application of DC series motors was in locomotives. This technology has been replaced by AC motors since 20 years. The latest generation of high speed trains use synchronous, permanent magnet motors.
With a proper soft drive you can go with an induction motor, but it depends. if power is small you can go to step motor also. But dc series motor's starting torque is high as expressed others.
DC Series motors have high starting torque but induction motors have wide range of speed control. So, If DC motor is used, then DC drives you can use, although it will be expensive and DC motors are tough to maintain than ac motors due to commutation Problem.
DC series motor would provide both the high starting torque and adjustable speed BUT beware that DC motors have high maintenance cost and also require AC-DC conversion. You could use other available options e.g. double wound induction motors etc, depending upon your requirements.
But today, there is no application where you cannot apply AC motors, asynchronous or synchronous. If the motor and the associated power electronics are correctly rated, you can have any starting torque you want.
The typical application of DC series motors was in locomotives. This technology has been replaced by AC motors since 20 years. The latest generation of high speed trains use synchronous, permanent magnet motors.
it depends on so much more than the simple requirements listed of high starting torque and variable speed. What kind of application are you using it for? Is it on an automobile (where you have DC already), a factory, and do you have the budget and/or space for a variable frequency drive. A synchronous servo motor gives great dynamic control and great starting torque per volume, but its speed range is limited (unless you're field weakening by the back EMF). Servo-motors are also the most expensive due to their position sensors and more intelligent drives
---->> by
---->> by
You may also like:
Overload protection: the soft starter has current control loop to track and detect of the changes of the electric motor current. Achieve overload protection by increasing overload current settings and inverse ...
First, specify that this is an isolated system with two generators feeding the same bus. Operation of an isolated system is different than a grid connected system, and the mode setting of the governors have to ...
Stiff voltage sources are not problematic as long as they don't get in the way of the solver's attempts to linearize the behavior of the circuit matrix via step size reduction. It is the highly nonlinear stiff ...
Variable frequency drives are electronic devices, they have stringent requirements in installation environment which is specified in its user manual normally. In exceptional circumstances, if it does not meet ...
Generally, electric motors are designed according to 50Hz power supply, its rated torque also in this frequency. Therefore, the speed adjustment under rated frequency called constant torque speed adjustment. ...
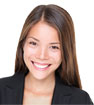
Featured
Like pumps, fans consume significant electrical energy while serving several applications. In many plants, the VFDs (variable ...
A frequency inverter controls AC motor speed. The frequency inverter converts the fixed supply frequency (60 Hz) to a ...
Motor starter (also known as soft starter, motor soft starter) is a electronic device integrates soft start, soft stop, ...
Soft starter allows the output voltage decreases gradually to achieve soft stop, in order to protect the equipment. Such as the ...
Soft Starter reduces electric motor starting current to 2-4 times during motor start up, reduces the impact to power grid during ...

In Discussion
PMSM initial rotor alignment: what is the correct strategy?
DCS
DTC vs. classic PWM vector VFD
unbalanced load distribution among three phases in a building
Connection between Reactive Power and Vibration
Difference between Numerical calculating and FEA almost %10 error, Why?
Pros and Cons of Self-priming Centrifugal Pumps
use of varistors in SPICE simulations
DCS
DTC vs. classic PWM vector VFD
unbalanced load distribution among three phases in a building
Connection between Reactive Power and Vibration
Difference between Numerical calculating and FEA almost %10 error, Why?
Pros and Cons of Self-priming Centrifugal Pumps
use of varistors in SPICE simulations