Home » Blog » Experience » Experience: Flyback
Experience: Flyback
My first SMPS design was a multiple output flyback. This was in 1976, when there were no PWM controllers. So I used a 556 (1/2 osc -30 kHz, and 1/2 PWM generator) plus used a 3904 NPN where the VBE was the reference and also provided gain for the error amp function. I hap-hazardly wound the windings on a 25 mm torroid. It ranglike a tank circuit. I quickly abandoned the transformer and after a year, and many hours on the bench, I had a production-grad SMPS.
Since it went into a private aircraft weather reader system, I needed an exterier SMPS which was a buck converter. I used an LM105 linear regulator with positive feedback to make it oscillate (one of nationals ap notes). It worked, but I soon learned that the electrolytic capacitors lost all of their capacitance at -25 deg C. It later worked with military-grade capacitors.
I had small hills of dead MOSFETs and the directly attached controllers. When the first power MOSFETs emerged in 1979, I blew-up so many that I almost wrote them off. They had some real issues with D-S voltage overstress. They have come a long way since.
As far as very wide range flyback converter, please dig-up AN1327 on the ONSEMI website. This describes a control strategy (fixed off-time, variable on-time) and the transformer design.
The processor to that was a 3W flyback that drove 3 floating gate drive circuits and had an input range of 85 VAC to 576 VAC. It was for a 3 phase industrial motor drive. The toughest area was the transformer. To meet the isolation requirements of the UL, and IEC, it would have required a very large core, and bobbin plus a lot of tape. The PCB had the dimensions of 50 mm x 50 mm and 9 mm thick A magnetics designer named Jeff Brown from Cramerco.com is now my magnetics God. He designed me a custom core and bobbin that was 10 mm high on basically an EF15 sized core. The 3 piece bobbin met all of the spacing requirements without tape. The customer was expecting a 2 - 3 tier product offering for the different voltage ranges, but instead could offer only one. They were thrilled.
Can be done, watch your breakdown voltages, spacings and RMS currents. I found that around 17 -20 watts is about the practical limit for an EF40 core before the transformer RMS currents get too high.
Since it went into a private aircraft weather reader system, I needed an exterier SMPS which was a buck converter. I used an LM105 linear regulator with positive feedback to make it oscillate (one of nationals ap notes). It worked, but I soon learned that the electrolytic capacitors lost all of their capacitance at -25 deg C. It later worked with military-grade capacitors.
I had small hills of dead MOSFETs and the directly attached controllers. When the first power MOSFETs emerged in 1979, I blew-up so many that I almost wrote them off. They had some real issues with D-S voltage overstress. They have come a long way since.
As far as very wide range flyback converter, please dig-up AN1327 on the ONSEMI website. This describes a control strategy (fixed off-time, variable on-time) and the transformer design.
The processor to that was a 3W flyback that drove 3 floating gate drive circuits and had an input range of 85 VAC to 576 VAC. It was for a 3 phase industrial motor drive. The toughest area was the transformer. To meet the isolation requirements of the UL, and IEC, it would have required a very large core, and bobbin plus a lot of tape. The PCB had the dimensions of 50 mm x 50 mm and 9 mm thick A magnetics designer named Jeff Brown from Cramerco.com is now my magnetics God. He designed me a custom core and bobbin that was 10 mm high on basically an EF15 sized core. The 3 piece bobbin met all of the spacing requirements without tape. The customer was expecting a 2 - 3 tier product offering for the different voltage ranges, but instead could offer only one. They were thrilled.
Can be done, watch your breakdown voltages, spacings and RMS currents. I found that around 17 -20 watts is about the practical limit for an EF40 core before the transformer RMS currents get too high.
You may also like:
Overcurrent protection uses as back-up protection for protection generators from faults between two windings of stator (two phases of stator). Setting of overcurrent protection depends from two settings: ...
Non-regenerative DC drives, also known as single-quadrant drives, rotate in one direction only & they have no inherent braking capabilities. Stopping the motor is done by removing voltage & allowing ...
What are the general guide lines for snubber circuit design in Inverter applications? When i referred the literature for snubber circuits for IGBT protection i found that we can either go for "individual" ...
I would like to share these tips with everybody.
A current mode controlled flyback converter always becomes unstable at low load due to the unavoidable leading edge current spike. It is not normally dangerous ...
Soft starters and variable frequency drives are two different purpose products. VFD is for AC motor speed control, it's not only change the output voltage but also change the frequency; Soft starter is a ...
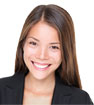
Featured
Like pumps, fans consume significant electrical energy while serving several applications. In many plants, the VFDs (variable ...
A frequency inverter controls AC motor speed. The frequency inverter converts the fixed supply frequency (60 Hz) to a ...
Motor starter (also known as soft starter, motor soft starter) is a electronic device integrates soft start, soft stop, ...
Soft starter allows the output voltage decreases gradually to achieve soft stop, in order to protect the equipment. Such as the ...
Soft Starter reduces electric motor starting current to 2-4 times during motor start up, reduces the impact to power grid during ...

In Discussion
how the mirrors of solar panels move, to stay in the direction of the sun?
Using Bridges for High Reliability Applications
How good are analogue hall sensors as a form of position control?
The smaller dimensions motors are in efficient
Non Contact sensor to detect direction of rotation of Fan blades
grounding
Transformers in Parallel: The Myth
earthing design
Using Bridges for High Reliability Applications
How good are analogue hall sensors as a form of position control?
The smaller dimensions motors are in efficient
Non Contact sensor to detect direction of rotation of Fan blades
grounding
Transformers in Parallel: The Myth
earthing design