Home » Blog » Experience » Page 2
Ahh I see the words machine tool and shop floor; now I can see where you guys are coming from. The type of machines that you talk about were controlled by relay logic and then when technology arrived the electrical drawings were probably "converted" into ladder logic. The techs had lots to do because you cannot translate relay based systems into ladder logic 100% successfully as they behave differently.
If I had a "critical" operation with a double-action cylinder, hydraulic or pneumatic, I'd put proximity sensors on both ends of travel, typically with small metal "marker" on the shaft. Each input "in series" with the "output” to each coil, time delayed to give the cylinder a chance to reach its destination. The "timer" feeds the "alarm." If you want to spend the money for a pressure switch (or transducer) on each solenoid output, that's a plus.
Many of the techniques contributed by others in the discussion address faults, but how do you address the "normal" things that can hold up an action such as waiting for a process condition to occur, such as waiting for a level/pressure/temperature to rise above/fall below a threshold or waiting for a part to reach a limit switch?
I once uprated a set of 3x 500KVA 11/.433kv ONAN transformers to 800KVA simply by fitting bigger radiators. This was with the manufacturers blessing. (not hermetically sealed - there were significant logistical difficulties in changing the transformers, so this was an easy option). Limiting factor was not the cooling but the magnetic saturation of the core at the higher rating. All the comments about uprating the associated equipment are relevant, particularly on the LV side.
Grounding (or Earthing) - intentionally connecting something to the ground. This is typically done to assist in dissipating static charge and lightning energy since the earth is a poor conductor of electricity unless you get a high voltage and high current.
A few years back, I had a devil of time getting some OPC Modbus TCP drivers to work with Modbus RTU to TCP converts. The OPC drivers could not handle the 5 digit RTU addressing. You need to make sure your OPC driver that you try actually works with your equipment.
We got by testing 3 different machines under no-load condition.
The 50 HP and 3 HP are the ones which behave abnormally when we apply 10% overvoltage. The third machine (7.5 HP) is a machine that reacts normally under the same condition.
What we mean by abnormal behavior is the input power of the machine that will increase dramatically under only 10% overvoltage which is not the case with most of the induction machines. This can be seen by the numbers given below.
Coming from a signal processing and communications theory background, but with some experience in power design, I can't resist the urge to chime in with a few remarks.
There are many engineering methods to deal with sources of interference, including noise from switching converters, and spread spectrum techniques are simply one more tool that may be applied to achieve a desired level of performance.
A system I have just completed was 24 containers + 3 buildings for storage with 76 conveyors, 3 drop-off and 3 loading points. Connection to ERP system and weigh scales to weigh trucks and send them to the correct bay. Local HMI on each bay ensured correct lorry goes to correct bay. Main conveyor runs are automatically selected. Manual option to run all conveyors to move grain around.
There being a lot more than 12 guidelines to follow. In my experience, there are plenty of people that can design a panel but if they haven't gone to the field with it then they haven't been able to learn from their design mistakes.The best thing you can do is start your design but you really need to be guided by an experienced designer.
My cable size and transformer size should give me maximum 3% on the worst 6% to 10%. If it is the single only equipment on the system then maybe you can tolerate 15%. If not, dip factor may affect sensitive equipment and lighting.
Remote diagnostic is a must now a days. All CNC machines must be able to undergo remote access to undergo diagnostic and it must be two way. The problem mostly with remote diagnostic is it has to be two way and you have to have a qualified technician or an operator who is well verse with machine operations and its features, always on your machine he must be trained on how to be able to recover from lost of communication and the most important is to be able to engage E-stop when needed.
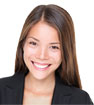
Featured
Like pumps, fans consume significant electrical energy while serving several applications. In many plants, the VFDs (variable ...
A frequency inverter controls AC motor speed. The frequency inverter converts the fixed supply frequency (60 Hz) to a ...
Motor starter (also known as soft starter, motor soft starter) is a electronic device integrates soft start, soft stop, ...
Soft starter allows the output voltage decreases gradually to achieve soft stop, in order to protect the equipment. Such as the ...
Soft Starter reduces electric motor starting current to 2-4 times during motor start up, reduces the impact to power grid during ...

In Discussion
how to select a voltage for a transmission line for about 300 miles and 1000MW
Generator and Transformer combination
Pump to evacuate warm air
Why Bucholz relay is used for transformer incipient fault detection?
I have been asked to relocate from my employer to other region
Doubts on I/O Count, Smart MCC, Motor control Philosphy..
Setting up 1 MW Hybrid Solar-Biomass Power Plant - Grid connected
Motor Space Heater requirement !
Generator and Transformer combination
Pump to evacuate warm air
Why Bucholz relay is used for transformer incipient fault detection?
I have been asked to relocate from my employer to other region
Doubts on I/O Count, Smart MCC, Motor control Philosphy..
Setting up 1 MW Hybrid Solar-Biomass Power Plant - Grid connected
Motor Space Heater requirement !