Home » Blog » Motor controls » Die-cast rotor design
Die-cast rotor design
The method of creating a die-cast rotor is as follows:
1. An assembly of steel laminations (which may or may not be grain-oriented) containing the openings for both rotor bars and ventilation (as required) is made and clamped together to form a cylindrical iron core.
2. The assembly is inserted into a mold, which has space both above and below the core for the end (shorting) ring assembly.
3. The molten conductor material (aluminum or copper, usually) is injected into the mold and allowed to flow through the bar openings. It also fills the end ring spaces.
4. The entire assembly is allowed to cool so that the conductor solidifies.
5. The "cast" core is then shrunk onto a steel shaft.
Now we have a "cast" rotor assembly, ready for bearings and mounting into machine.
1. An assembly of steel laminations (which may or may not be grain-oriented) containing the openings for both rotor bars and ventilation (as required) is made and clamped together to form a cylindrical iron core.
2. The assembly is inserted into a mold, which has space both above and below the core for the end (shorting) ring assembly.
3. The molten conductor material (aluminum or copper, usually) is injected into the mold and allowed to flow through the bar openings. It also fills the end ring spaces.
4. The entire assembly is allowed to cool so that the conductor solidifies.
5. The "cast" core is then shrunk onto a steel shaft.
Now we have a "cast" rotor assembly, ready for bearings and mounting into machine.
You may also like:
There are two important different parameters as far as the disconnection/connection of Electrical utilities is concerned.
- Breaking capacity.
- Making Capacity.
For flyback & boost applications, powder cores such as Kool-mu, Xmu, etc... are usually best performing and lowest cost. Even these may need to be gapped and if CCM operation is required, a "stepped-gap" ...
With a heavily discontinuous mode flyback design, the transformer's ac portion of current can be larger than the dc portion. When a high perm material is used for the transformer core, the required gap can be ...
When operating an AC machine on a variable frequency drive, the most common approach is to mimic the DC curves. This is done by using a constant volt/hertz ratio until a "base" speed is achieved at rated ...
The aforementioned types of Circuit Breakers are used in LV System and generally based on the same operating principle.
MCB and MCCB/ICCB have a bimetal heater for overload which releases the Contact s while ...
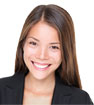
Featured
Like pumps, fans consume significant electrical energy while serving several applications. In many plants, the VFDs (variable ...
A frequency inverter controls AC motor speed. The frequency inverter converts the fixed supply frequency (60 Hz) to a ...
Motor starter (also known as soft starter, motor soft starter) is a electronic device integrates soft start, soft stop, ...
Soft starter allows the output voltage decreases gradually to achieve soft stop, in order to protect the equipment. Such as the ...
Soft Starter reduces electric motor starting current to 2-4 times during motor start up, reduces the impact to power grid during ...

In Discussion
How would you code this in logic controller?
Process Dynamic Control
Horizontal and vertical electric motor Difference?
What is Stuck Breaker Protection?
Cooling tower automation
Solar Panel Made In America Requirements
SFC For Stating a Gas turbine
Circuit Breaker Analyzer in Preventive Maintenance Plan
Process Dynamic Control
Horizontal and vertical electric motor Difference?
What is Stuck Breaker Protection?
Cooling tower automation
Solar Panel Made In America Requirements
SFC For Stating a Gas turbine
Circuit Breaker Analyzer in Preventive Maintenance Plan