I had small hills of dead MOSFETs and the directly attached controllers. When the first power MOSFETs emerged in 1979, I blew-up so many that I almost wrote them off. They had some real issues with D-S voltage overstress. They have come a long way since.
I tell customers that at least 50% of the design effort is the layout and routing by someone who knows what they are doing. Layer stackup is very critical for multiple layer designs. Yes, a solid design is required. But the perfect design goes down in flames with a bad layout. It is best in one of his early books that you have to "think RF" when doing a layout.
I have been designing power supplies for over 15 years now. We do mostly off line custom designs ranging from 50 to 500W. Often used in demanding environments such as offshore and shipping.
I think we are the lucky ones who got the chance to learn designing power supplies using the simple topologies like a flyback or a forward converter. If we wanted to make something fancy we used a push-pull or a half bridge.
I work across the scale of power electronics in voltages and currents. From switchers of 1W for powering ICs to 3kW telco power supplies up to multi-megawatt power converters for reactive power control in AC transmission networks and into power converters for high voltage transmission.
I never just put power to a first prototype and see what happens. Smoke and loud sounds are the most likely result and then you just know that something was not perfect. So how would you test the next prototype sample?
After that he certainly never forgot this key lesson: never attempt to measure FET current by putting a current probe in its source--- put it on the drain side. It was that simple. The same unit never exploded after that, just to complete the story.
I remember my very first power supply. They threw me in the deep end in 1981 building a multi-output 1 kW power supply. I was fresh from college, thought i knew everything, and consumed publications voraciously to learn more. Exciting times.
With a heavily discontinuous mode flyback design, the transformer's ac portion of current can be larger than the dc portion. When a high perm material is used for the transformer core, the required gap can be quite large in order to reach the low composite permeability required while the core size will likely be driven by winding and core loss considerations rather than just simply avoiding saturation.
For flyback & boost applications, powder cores such as Kool-mu, Xmu, etc... are usually best performing and lowest cost. Even these may need to be gapped and if CCM operation is required, a "stepped-gap" is preferred to allow a large load compliance. Center stepped gaps reduce the fringe flux greatly as there is never a complete gap, only localized saturation.
Determination of required grounding impedance is based on determination of coefficient of grounding which represents ratio of maximum phase voltage at phases which aren't exposed by fault and line voltage of power network:
Large machines are - generally speaking - made of pieces (segments) because the circle for the stator and/or rotor core is too large to manufacture from a single sheet. This leads to some breaks in the magnetic flux path symmetry, both in the radial (right angles to the shaft) and axial (parallel to the shaft) directions.
A graphical impedance analyzer with good phase resolution is a must. Some brands have all the bells and whistles, but not the phase resolution necessary to accurately measure high Q (100+) components over the instrument's full frequency range (which should extend at least into the low megahertz).
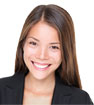
Featured
Like pumps, fans consume significant electrical energy while serving several applications. In many plants, the VFDs (variable ...
A frequency inverter controls AC motor speed. The frequency inverter converts the fixed supply frequency (60 Hz) to a ...
Motor starter (also known as soft starter, motor soft starter) is a electronic device integrates soft start, soft stop, ...
Soft starter allows the output voltage decreases gradually to achieve soft stop, in order to protect the equipment. Such as the ...
Soft Starter reduces electric motor starting current to 2-4 times during motor start up, reduces the impact to power grid during ...

In Discussion
Are there any zero installation, Windows based, stand-alone HMIs?
Should SCADA PC, HMI, PLC, DCS be on the same existing IT NETWORK
what is the difference of turbine impellers and propeller agitators?
Bode diagram
Spur growth and demand for Electric Motors in India.
question: I am in a debate concerning motion.
Problems overcoming check valve on fire pump system
ONE of my diesel generator 1400kva trips down
Should SCADA PC, HMI, PLC, DCS be on the same existing IT NETWORK
what is the difference of turbine impellers and propeller agitators?
Bode diagram
Spur growth and demand for Electric Motors in India.
question: I am in a debate concerning motion.
Problems overcoming check valve on fire pump system
ONE of my diesel generator 1400kva trips down