1) Mechanical Simulations – Via various solid modeling tools and cad
programs; tooling, moving mechanisms, end-effectors… are designed with
3D visualizations, connecting the modules to prevent interference, check
mass before actual machining…
2) Electronics Simulations – This type of simulations are either related to the manufacturers of "specific instrumentations" used in automation industry (ultrasonic welders, laser marking systems,…) or the designers of circuit boards.
3) Electrical & Controls Simulations.
2) Electronics Simulations – This type of simulations are either related to the manufacturers of "specific instrumentations" used in automation industry (ultrasonic welders, laser marking systems,…) or the designers of circuit boards.
3) Electrical & Controls Simulations.
If you look back over history you will find how things started out from the early engineers and scientists looking at materials and developing systems that would meet their transmission goals. I recall when drives (essentially ac/dc/ac converters) had an upper limit around 200 to 230 volts).
A 1:1 ratio transformer is primarily used to isolate the primary from the secondary. In small scale electronics it isolates the noise / interference collected from the primary from being transmitted to the secondary. In critical care facilities it can be used as an isolation transformer to isolate the primary grounding of the supply from the critical grounding system of the load (secondary).
Grounding (or Earthing) - intentionally connecting something to the ground. This is typically done to assist in dissipating static charge and lightning energy since the earth is a poor conductor of electricity unless you get a high voltage and high current.
SCADA will have a set of KPI's that are used by the PLCs/PACs/RTUs as standards to compare to the readings coming from the intelligent devices they are connected to such as flowmeters, sensors, pressure guages, etc.
HMI is a graphical representation of your process system that is provided both the KPI data and receives the readings from the various devices through the PLC/PAC/RTUs.
You know standards for the electronic industry have been around for decades, so each of the interfaces we have discussed does have a standard. Those standards may be revised but will still be used by all segments of our respective engineering disciplines.
The concept of home automation on a global scale is a good concept. How to implement such a technology on a global scale is an interesting problem, or I should say issues to be resolved. Before global approval can be accomplished the product of home automation may need a strategy that starts with a look at companies that have succeeded in getting global approval of their products.
A few years back, I had a devil of time getting some OPC Modbus TCP drivers to work with Modbus RTU to TCP converts. The OPC drivers could not handle the 5 digit RTU addressing. You need to make sure your OPC driver that you try actually works with your equipment.
You already know from your engineering that higher voltages results to less operational losses for the same amount of power delivered. The bulk capacity of 3000MW has a great influence on the investment costs obviously, that determines the voltage level and the required number of parallel circuit.
The generator designers will have to determine the winding cross section area and specific current/mm2 to satisfy the required current, and they will have to determine the
required total flux and flux variation per unit of time per winding to
satisfy the voltage requirement.
We got by testing 3 different machines under no-load condition.
The 50 HP and 3 HP are the ones which behave abnormally when we apply 10% overvoltage. The third machine (7.5 HP) is a machine that reacts normally under the same condition.
What we mean by abnormal behavior is the input power of the machine that will increase dramatically under only 10% overvoltage which is not the case with most of the induction machines. This can be seen by the numbers given below.
Equivalent active power losses during electrical motor's testing in no-load conditions contain next losses:
1. active power losses in the copper of stator's winding which are in direct relation with square of no-load current value: Pcus=3*Rs*I0s*I0s,
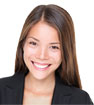
Featured
Like pumps, fans consume significant electrical energy while serving several applications. In many plants, the VFDs (variable ...
A frequency inverter controls AC motor speed. The frequency inverter converts the fixed supply frequency (60 Hz) to a ...
Motor starter (also known as soft starter, motor soft starter) is a electronic device integrates soft start, soft stop, ...
Soft starter allows the output voltage decreases gradually to achieve soft stop, in order to protect the equipment. Such as the ...
Soft Starter reduces electric motor starting current to 2-4 times during motor start up, reduces the impact to power grid during ...

In Discussion
INERTIZATION OF FLAMMABLE LIQUID STORAGE TANKS
Are cloud computing and SCADA a good combo?
Replace transformer's circuit breaker with fused disconnector switch
how we can differentiate faults and disturbances in a power system??
In what way is OPC better for PLC-SCADA comms?
High saturation flux ferrite for PFC Choke
why the ct has turns ratio 1 or 5 in the secondary side irrespective of the primary side?
How the easier way to calculate short circuit rating (kA) for the AC?
Are cloud computing and SCADA a good combo?
Replace transformer's circuit breaker with fused disconnector switch
how we can differentiate faults and disturbances in a power system??
In what way is OPC better for PLC-SCADA comms?
High saturation flux ferrite for PFC Choke
why the ct has turns ratio 1 or 5 in the secondary side irrespective of the primary side?
How the easier way to calculate short circuit rating (kA) for the AC?