Is there a way of connecting a three phase pressure control switch on a three phase motor. Also is there a three phase float switch for a three phase submersible pump i know of a single phase switch.
The switch only needs to have a single contact since you use a three-phase motor controller to operate the motor. The switch is wired into the low voltage contactor coil circuit to turn the motor on and off.
The switch only needs to have a single contact since you use a three-phase motor controller to operate the motor. The switch is wired into the low voltage contactor coil circuit to turn the motor on and off.
A typical variable torque application would be a centrifugal pump. A typical constant torque application would be a conveyor, and there are positive displacement pumps that are also constant torque. Have a talk with a mechanical engineer, get them to show you curves and explain.
1. How does this affect the vector group (YNd1) of the transformer? Will it be changed to YNd11?
2. Will it make any difference as far as the vector group is concerned if instead of phase A and C, phase B and C were swapped on both ends of the transformer?
3. The transformer protection relay is configured for YNd1 group, and it is reading negative phase sequence current (ACB instead of ABC). Changing the vector group configuration will solve the problem?
4. Relay is used for differential protection (percentage differential) of the transformer.
Will this negative phase sequence affect normal operation of the transformer in any way?
2. Will it make any difference as far as the vector group is concerned if instead of phase A and C, phase B and C were swapped on both ends of the transformer?
3. The transformer protection relay is configured for YNd1 group, and it is reading negative phase sequence current (ACB instead of ABC). Changing the vector group configuration will solve the problem?
4. Relay is used for differential protection (percentage differential) of the transformer.
Will this negative phase sequence affect normal operation of the transformer in any way?
In any electrical system, we limit the neutral grounding to 1 or 2 locations at the power source, eg, the star-points of generators or transformers. By keeping the grounded neutrals at the power source, earth leakage current will be flowing radially from the power source to the point of short-circuit at downstream. In this way the direction of earth fault current flow can be easily identified and the earth fault protection relays in the distribution system can easily be coordinated.
When two transformers are in a parallel group, a transformer with a higher tap position will typically have a higher (LV side) no-load voltage than the other one with a lower tap position. These unequal no-load voltages (unequal tap positions) will cause a circulating current to flow through the parallel connected transformers.
For small circuit breakers we can do the test of Magnetic protection behavior by using "Injection Current Apparatus", and suppose the CB's results were good, do you think it's enough? I'm sure not, because by this apparatus we can inject the necessary current with a very low voltage value (5-15V), so, do you think that the arc will be the same if we have the same current but with "400V"?
The aforementioned types of Circuit Breakers are used in LV System and generally based on the same operating principle.
MCB and MCCB/ICCB have a bimetal heater for overload which releases the Contact s while for short circuit the trip / electromagnet hammers itself against moving contacts. The arc created by breaking contacts is extinguished in an arc chamber.
Transformers are rated in {VA, kVA, MVA etc.} due to flows of active and reactive power through transformer. In case of transformer we have active power losses as consequence of existence inside resistance of windings (primary and secondary) and existence of active losses of ferromagnetic core and other side we have reactive power losses as consequence of existence losses of magnetic flux (primary and secondary) and existence of reactive power losses of ferromagnetic core.
Its beneficial to opt for the AC Drives as it supports SLVC [ VFD gives almost servo-like torque at low rpms if you give it encoder feedback ], multiple motors can be accessed, torque requirement can be met if required, power dips can be sustained using VFD's.
The harmonics are created by the loads that the transformer supplies power to. If your loads include a high percentage of electronic loads like IT equipment, electronic ballast lighting, electronic motor controls, etc., there can be a very high amount of harmonics that circulate back to the transformer. The harmonics create an increase in the neutral currents.
I am assuming that the trip circuit is floating DC (ungrounded). If so, the moisture could be causing a "sneak" circuit, otherwise known as a "hot short" in the tripping circuit, which essentially bypasses the sensing relay contacts and actuates the tripping relay coil. I would check the cabling between the sensing relay contacts and the trip relay coil and the cabling on the hot side of the sensing relay contacts for insulation problems.
This could be internal corona discharge. The switchgear should be de-energized and closely examined. That means pump out the SF6 and take it apart. Examine all insulating components.
Especially if the sound can be localized to portions of the switchgear which do not have bushings for connection to overhead lines. Even if the sound is in the area of air bushings, deenergizing will allow more in-depth inspection and addressing any sharp edges or cracked insulators, etc.
Especially if the sound can be localized to portions of the switchgear which do not have bushings for connection to overhead lines. Even if the sound is in the area of air bushings, deenergizing will allow more in-depth inspection and addressing any sharp edges or cracked insulators, etc.
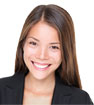
Featured
Like pumps, fans consume significant electrical energy while serving several applications. In many plants, the VFDs (variable ...
A frequency inverter controls AC motor speed. The frequency inverter converts the fixed supply frequency (60 Hz) to a ...
Motor starter (also known as soft starter, motor soft starter) is a electronic device integrates soft start, soft stop, ...
Soft starter allows the output voltage decreases gradually to achieve soft stop, in order to protect the equipment. Such as the ...
Soft Starter reduces electric motor starting current to 2-4 times during motor start up, reduces the impact to power grid during ...

In Discussion
electrical part designing
How to become a professional in PV system?
Power Transducer to measure output power Transformer
Is heat gain in centrifugal pumps the result of bearing friction alone?
Surge protection device for control cabinet in industrial yard?
Problem with interfacing rs485 cable with PC
Energy Storage at Grid Level
Minimum Short circuit Ik min in a 155kV network
How to become a professional in PV system?
Power Transducer to measure output power Transformer
Is heat gain in centrifugal pumps the result of bearing friction alone?
Surge protection device for control cabinet in industrial yard?
Problem with interfacing rs485 cable with PC
Energy Storage at Grid Level
Minimum Short circuit Ik min in a 155kV network